摘要:飞轮高强度螺栓在安装时断裂,断口通过宏观、电镜扫描、能谱分析等均未发现异常现象,随后进行微观检验方法发现螺栓断裂磨面有裂纹存在。故对裂纹来源进行了探究,结果表明断裂螺栓磨面裂纹来源于在线切割制样过程中运丝速度过快、冷却液冷却不充分、从而受热导致裂纹产生。为避免以后裂纹的再次出现,建议将线切割机切割频率参数调至合适的频率、使用水基切削液、深磨试样等方法。
关键词:飞轮;高强度;线切割;深磨试样
某公司是生产飞轮高强度螺栓的专业厂家,在安装过程中出现规格为M10×1.25×28螺栓螺纹杆部发生断裂现象。该断裂螺栓材料为SCM440,机械性能等级为10.9级,硬度为39.0HRC-44.0HRC。该断裂螺栓宏观形貌见图1。样品螺栓在安装时从螺纹杆部断裂,扭力矩为91N·m。为查清螺栓断裂磨面的原因,防止类似事件的发生,对断裂螺栓进行了电镜扫描,能谱及理化检验分析。
.jpg)
图1 宏观形貌及断裂部位
1 理化检验
1.1宏观检验
该螺栓断裂于螺纹杆部,其断口宏观形貌见图1。螺栓断口垂直于轴线,整个断口宏观上可分为三个区:①断裂源区,处于断口的边缘,螺纹根部。②放射区,为快速的断裂区,呈现明显的放射状条纹特征,放射区面积较大,占断口总面积的60%~70%。瞬间断裂区,处于断口的中心偏左,并与断裂源呈45°角,这些特征表明该螺栓断口为典型的在扭转载荷作用下发生的混合型断裂,以脆性断裂为主。
1.2 断口分析
运用EVO18扫描电子显微镜对螺栓断口进行微观形貌观察和分析,电镜下观察断口为撕裂准解理和韧窝状塑性混合性断裂(见图2、3)。
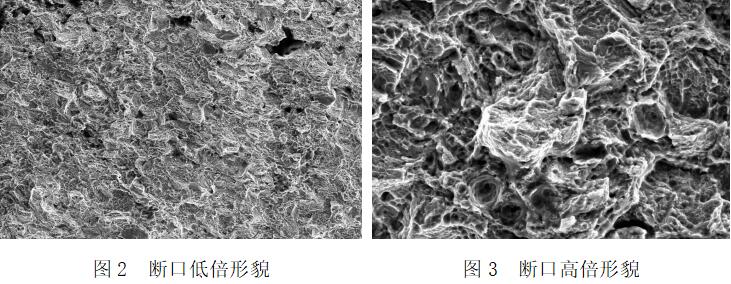
1.3 化学成分分析
运用MAXxLMM05直读光谱分析仪进行化学成分分析,按(GB/T4336-2016 碳素钢和中低合金钢 多元素含量的测定 火花放电原子发射光谱法),结果见表1,可知螺栓的化学成分满足协议SCM440的技术要求。
表1化学成分分析结果(质量分数)%
元素
|
C
|
S
|
P
|
Mn
|
Si
|
Cr
|
Ni
|
Mo
|
标准值
|
0.38~0.43
|
≤0.030
|
≤0.030
|
0.60~0.90
|
0.15~0.35
|
0.90~1.20
|
≤0.25
|
0.15~0.30
|
实测值
|
0.399
|
0.0070
|
0.0195
|
0.65
|
0.218
|
0.948
|
0.0208
|
0.197
|
1.4金相检验
对断口进行纵向线切割,磨制、抛光后,制成金相试样在光学显微镜下观察,根据GB/T10561-2005/ISO4967:1998(E)实际检验A法,使用ISO评级图评定,对钢中非金属夹杂物进行评级,断裂螺栓的夹杂物级别为:硫化物类级别:0.5级(细系),氧化铝类级别:0.5级(细系),硅酸盐类级别:0.5级(细系),球状氧化物类级别:1.0级(细系)。用体积分数为4%的HNO3 酒精溶液侵蚀后,用光学显微镜、扫描电镜及能谱仪分析断裂螺栓的显微组织。在光学显微镜下观察螺栓表层及芯部显微组织均为正常的细小、均匀的仍保留针状马氏体形态特征的回火索氏体组织;组织中存在数条疑似裂纹形态现象,沿晶分布,(见图4、5)。用扫描电镜及能谱仪对疑似裂纹痕迹区域进行分析,痕迹区域成分主要为Fe、Cr、Mn元素,为基体组织内部正常元素,非外界物或者非金属夹杂物质(见图6、7、8、9、10、11和表2、表3)。
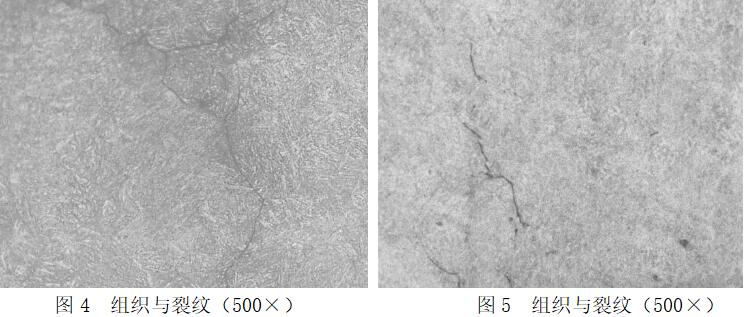
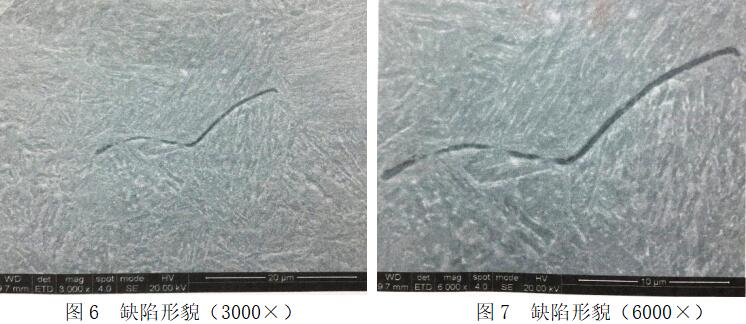
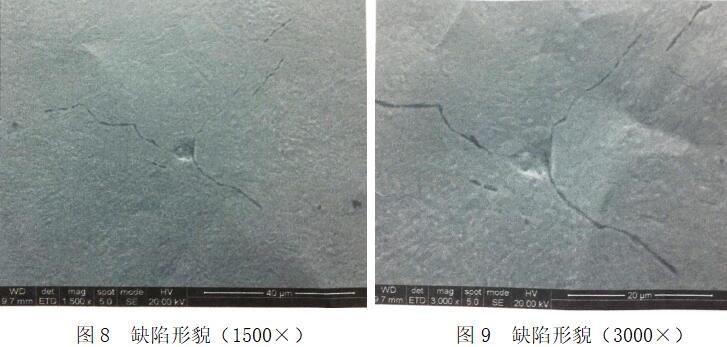
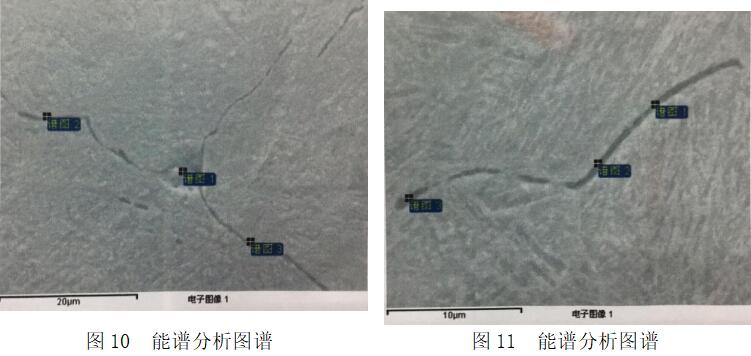
谱图
|
C%
|
Cr%
|
Fe%
|
谱图1
|
7.63
|
1.11
|
91.26
|
谱图2
|
——
|
1.17
|
98.83
|
谱图3
|
7.91
|
1.25
|
90.84
|
谱图
|
C%
|
Mn%
|
Fe%
|
谱图1
|
1.32
|
2.17
|
96.51
|
谱图2
|
1.04
|
1.48
|
97.47
|
谱图3
|
1.06
|
——
|
98.94
|
表2 能谱分析元素重量百分比表3 能谱分析元素重量百分比
将其扫描过分析的试样磨面进行一次粗抛光和一次精抛光,试样磨面的疑似裂纹均已经不存在(见图12、13)。
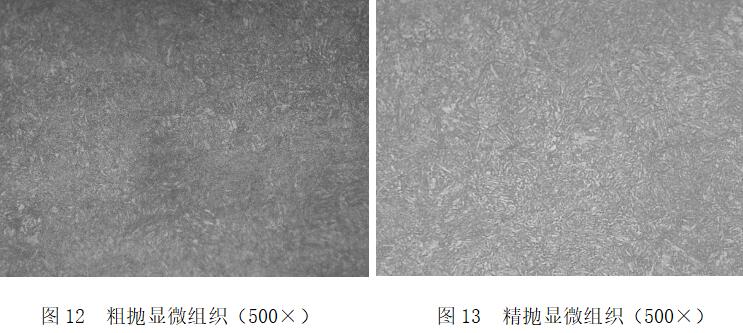
1.5硬度测试
用HR-150A洛氏硬度计对螺栓断口横截面,从螺栓表面至芯部进行硬度测试,其结果(见表4),结果显示硬度较均匀,表面硬度在35.9HRC~37.3HRC范围,平均值为 36.5HRC,芯部硬度为36.3HRC~38.3HRC,平均值为37.1HRC。
表4硬度测试结果
测试部位
|
实测值(HRC)
|
平均值(HRC)
|
表面
|
36.6
|
37.3
|
36.0
|
36.6
|
35.9
|
36.5
|
芯部
|
38.3
|
36.3
|
37.0
|
37.4
|
36.4
|
37.1
|
2 寻找裂纹来源
为探究断裂螺栓磨面疑似裂纹来源,将装机完好的螺栓抽取5件反复从人、机、料、法、环多方面进行分析验证,具体验证分析如下:
2.1 相同设备、相同人员、相同环境、不同方法下验证
对1#螺栓采用原有线切割机进行纵向切割,原有人员进行金相制样,改变磨样方法,分四次逐层由表至里进行磨样,抛光后用体积分数为4%的HNO3酒精溶液侵蚀后,用光学显微镜分析螺栓的显微组织,观察螺栓表层及芯部显微组织均为正常细小、均匀的仍保留针状马氏体形态特征的回火索氏体组织;前三次磨样都存在数条疑似网状裂纹形态现象,沿晶分布。第四次未见疑似裂纹形态现象,见图14、15、16、17。
2.2 相同设备、不同人员、相同环境、不同方法下验证
对2#螺栓采用原有线切割机进行纵向切割,不同人员进行金相制样,改变磨样方法,分四次逐层由表至里进行磨样,抛光后用体积分数为4%的HNO3酒精溶液侵蚀后,用光学显微镜分析螺栓的显微组织,观察螺栓表层及芯部显微组织均为正常细小、均匀的仍保留针状马氏体形态特征的回火索氏体组织;同样前三次磨样仍存在数条疑似网状裂纹形态现象,沿晶分布。第四次未见疑似裂纹形态现象,见图18、19、20、21。
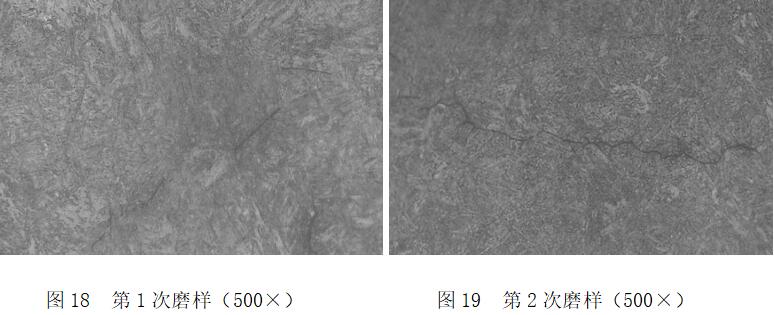
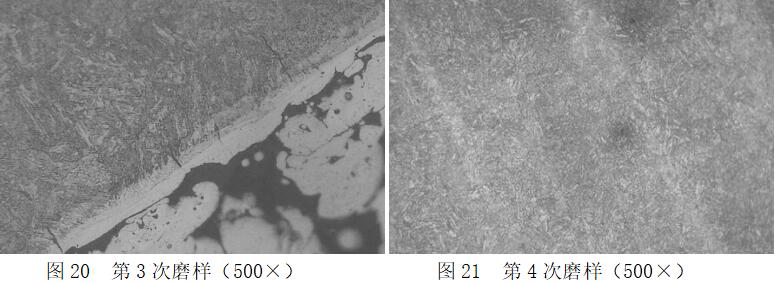
2.3 不同设备、相同人员、不同环境、相同方法下验证
对3#螺栓采用不同实验室线切割机进行纵向切割,由原有人员分两次逐层由表至里进行磨样,抛光后用体积分数为4%的HNO3酒精溶液侵蚀后,用光学显微镜分析螺栓的显微组织,观察螺栓表层及芯部显微组织均为正常细小、均匀的仍保留针状马氏体形态特征的回火索氏体组织;未见疑似裂纹形态现象。见图22、23。
通过对1#、2#、3#螺栓采用以上方法进行反复验证后,发现不同线切割机之间切割频率参数设置不一致、使用的冷却液不一致。继续对4#和5#螺栓进行验证。
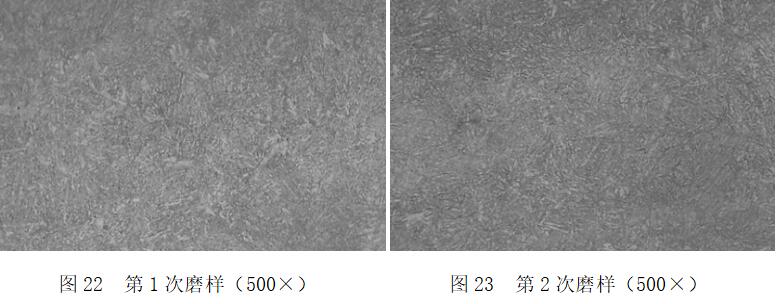
2.4 相同设备、相同人员、相同环境、相同方法下验证
对4#螺栓采用原有线切割机设备,将切割频率调至25Hz,更换冷却液后进行纵向切割,原有人员进行金相制样,分两次逐层由表至里进行磨样,抛光用经体积分数为4%的HNO3酒精溶液侵蚀后,用光学显微镜分析螺栓的显微组织,观察螺栓表层及芯部显微组织均为正常细小、均匀的仍保留针状马氏体形态特征的回火索氏体组织;未见疑似裂纹形态现象。见图24、25。
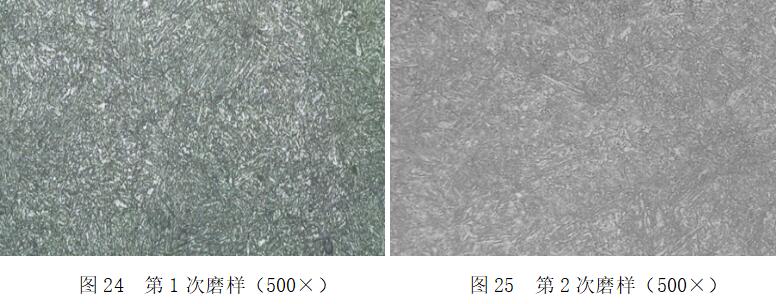
2.5 相同设备、不同人员、相同环境、相同方法下验证
对5#螺栓采用原有线切割机设备,将切割频率调至25Hz,更换冷却液后进行纵向切割,不同人员进行金相制样,分两次逐层由表至里进行磨样,抛光后用体积分数为4%的HNO3酒精溶液侵蚀后,用光学显微镜分析螺栓的显微组织,观察螺栓表层及芯部显微组织均为正常细小、均匀的仍保留针状马氏体形态特征的回火索氏体组织;未见疑似裂纹形态现象。见图26、27。
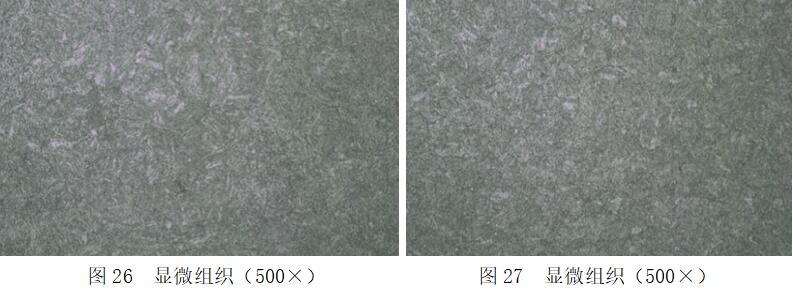
3 综合分析及结论
(1)由于断裂螺栓失效后,在做失效分析过程中发现螺栓断裂面存在网状疑似裂纹痕迹,能谱分析疑似裂纹痕迹区域成分为基体本身材质成分,非外来物质或者原材料本身的非金属夹杂物。
(2)为探究断裂螺栓磨面疑似裂纹来源,将装机完好的螺栓抽取5件反复从人、机、料、法、环多方面进行分析验证,样品抛光腐蚀后疑似裂纹痕迹出现可有可无现象。由此可见,通过不同人员,不同设备,不同的制样方法,不同的切削液反复验证,总结得出,线切割机在切割时频率过快,切削液不能快速冷却,导致螺栓切面受热,改变了组织,出现了表面微裂纹现象。
(3)为避免此类现象发生,建议将线切割机切割频率参数调至合适的频率、使用水基切削液、深磨试样等方法。
参考文献
[1]李炯辉主编金属材料金相图谱[M]北京机械工业出版社2006.6
[2]GB/T3098.1-2010紧固件机械性能 螺栓、螺钉和螺柱[S]
[3]钟群鹏,赵子华.断口学[M].哈尔滨工业大学出版社,2008