李海峰
(陕西宝光真空电器股份有限公司,陕西 宝鸡 721006)
摘 要:对不同批次的材料对比试验,排除影响不锈钢零件平面度因素,找到影响平面度的关键点;通过对模具的间隙调整和车制夹具的改进,从根本上解决平面度,满足生产要求,达到降本增效的目的。
关键词:模具 间隙 校平 平面度 成本
引 言:不锈钢零件的平面度一直困扰着车间,为了解决零件的平面度,我们以典型动盖板为试验突破口进行试验。通过对该零件每个环节试验进行分析。验证整形、退火等工序的必要性,以及加筋改变形状和调整模具间隙为小间隙等试验后。确定了合理的模具间隙和车工车制家具,总结出合理的不锈钢零件加工方式。新的加工方法及工艺,不仅提高了零件质量,也缩短零件的加工周期。
一、出现的问题
目前,车间加工不锈钢零件要加校平工序,校平工序效率低,返修次数多,它不仅影响车间的生产效率,而且加工成本大大增加(校平工时为0.7分/个);同时,由于材料的时效性,零件会在超过时效时间之后出现应力释放造成零件尺寸反弹甚至零件变形,影响装配质量和效果。
怎样解决零件的稳定性、平面度、加工效率及降低加工成本等问题已刻不容缓。这些问题制约公司发展,是车间,乃至公司急需解决的课题。
二、解决发现和实验步骤
为了解决不锈钢零件的平面度,试验以典型动盖板(图1)为突破口,该零件加工工艺为:落料—去毛刺—清洗—引深—整形—冲孔—车工。我们对该零件的加工工艺、生产模具结构、模具间隙及装夹方式系统分析和对来料的碾压方向和料厚进行观察和测量,确定试验方法和步骤。
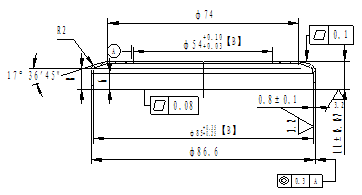
图1(平面度0.08mm和同轴度0.3mm)
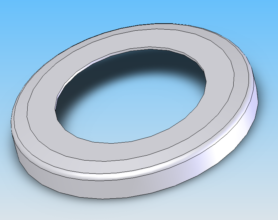
图2(该图为零件实体图)
2.1来料问题及模具保压
起初,我们怀疑来料的碾压方向影响零件的平面度。为此,我们对每片圆片料的碾压方向做标记,根据圆片料的标记规定在零件冲压过程片料摆放在模具不同位置,发现片料无论碾压方向一致和碾压方向没有规律时生产出的零件基本上一样,零件的平面度和椭圆度还是很难保证,所以实验说明板料的碾压方向对零件的平面度影响不是很大。
设备加工典型动盖板冲压为13个/分钟,我们为了提高该零件的稳定性,让零件冲压成型后在模具中保持一段时间(不同的时间段出现的零件也基本一样),试验后发现模具保压也不能解决问题。
2.2加工工艺试验
我们根据典型动盖板的加工工艺。为了释放应力,提高零件的稳定性,我们在零件的生产过程中加入退火工序和调整整形工序顺序,并制定了八条新的加工工艺,见表1。
实验1
|
落料
|
引伸
|
冲孔
|
车工
|
|
|
实验2
|
落料
|
退火
|
引伸
|
冲孔
|
车工
|
|
实验3
|
落料
|
引伸
|
退火
|
冲孔
|
车工
|
|
实验4
|
落料
|
引伸
|
退火
|
冲孔
|
整形
|
车工
|
实验5
|
落料
|
退火
|
引伸
|
整形
|
冲孔
|
车工
|
实验6
|
落料
|
引伸
|
退火
|
整形
|
冲孔
|
车工
|
实验7
|
落料
|
引伸
|
退火
|
冲孔
|
整形
|
车工
|
实验8
|
落料
|
引伸
|
冲孔
|
退火
|
整形
|
车工
|
表1
从表1可以看出,退火工序有无对零件的平面度影响不是很大,此类零件生产必须加整形工序。
通过试验,我们确定了此类零件生产工艺为:落料—引伸—整形—冲孔—车工
2.3调整模具间隙和车工装夹方式
经过上述的试验,我们目光回到了模具的上,根据对所有来料的料厚测量,发现料厚基本上在0.91mm~0.94mm之间,发现这个问题后,我们马上对模具间隙调整,并设计车工装夹夹具及制定车工车制方法。
2.3.1小间隙模具试验过程
我们根据料厚为0.91mm~0.94mm,给出模具尺寸,引深凹模尺寸为Φ86.88mm,引深凸模Φ84.87mm。这样的的话,模具间隙0.13mm~0.19mm,我们用新模具和新的车工加工方法对不同批次的材料试验。
试 验1:
2010年12月28日,零件加工工艺为:落料—去毛刺—清洗—引深—整形—冲孔—车工,材料批号:03325100,料厚为0.94mm~0.95mm(料厚基本为0.94mm), 本批零件椭圆度小于0.15mm。试验2000件.
结果是:12月29日累计送出1950件,85%平面度小于0.08mm,近15%平面度小于0.1mm,发现6件平面度在0.1mm~0.12mm范围.
试 验2:
零件加工工艺为:落料—去毛刺—清洗—引深—冲孔—车工
材料批号:03325100,料厚为0.94mm~0.95mm(料厚基本为0.94mm),试验50件,
结果是:送出50件,35件平面度小于0.1mm,10件平面度在0.1mm~0.12mm范围,5件平面度在0.12mm~0.15mm范围。合格率占70%。
试 验3:
2010年12月30日 材料批号:0332510076, 试验357件,料厚为0.94mm~0.95mm(料厚基本为0.94mm).
结果是:85%平面度小于0.08mm, 15%平面度小于0.1mm,
试 验4:
材料批号:0852510082,料厚为0.90mm~0.92mm(料厚基本为0.90mm),试验2000件,本批零件椭圆度小于0.2mm。
结果是:送出2000件平面度小于0.1mm的1795件,其中平面度在0.08mm之内的占60%,205件其余平面度在0.10mm~0.12mm,合格率占89.75%。
试 验5:
材料批号:0332511002,料厚为0.91mm~0.925mm(料厚基本为0.91mm),试验2400件,本批零件椭圆度小于0.2mm。
结果是:发现210件平面度在0.12mm~0.15mm范围. 其余平面度小于0.08mm。
2.3.小间隙试验
我们再次调整模具间隙:引深凹模尺寸为Φ87.02mm,引深凸模Φ85.1mm。那么模具间隙为0.04mm~0.1mm,零件加工工艺为:落料—去毛刺—清洗—引深—整形—冲孔—车工,车工加工零件的夹具及工艺与试验1一致。
试 验:
材料批号:0332511002,料厚为0.91mm~0.925mm(料厚基本为0.91mm),试验210件,引深后零件椭圆度小于0.15mm。
结果为:120件平面度小于0.08mm,19件平面度小于0.10mm,
经过两种间隙的试验,发现模具间隙太小对冲压设备和模具损耗大,缩短了设备与模具的寿命,合理的间隙是保证零件平面度和椭圆度的基础。见表2
实验
次数
|
工艺
|
材料
牌号
|
投产
数量
|
平面度<0.08mm
|
平面度<0.1mm
|
平面度<0.12mm
|
平面度<15mm
|
料厚
|
1
|
1
|
03325100
|
2000
|
85%
|
近15%
|
6件
|
|
约0.95mm
|
2
|
2
|
03325100
|
50
|
0
|
35件
|
10件
|
5件
|
约0.95mm
|
3
|
1
|
0332510076
|
357
|
85%
|
15%
|
|
|
约0.95mm
|
4
|
1
|
0852510082
|
2000
|
60%
|
|
205件
|
0
|
约0.92mm
|
5
|
1
|
0332511002
|
2400
|
91.25%
|
0
|
0
|
210件
|
约0.92mm
|
表2
注 工艺1:落料—去毛刺—清洗—引深—整形—冲孔—车工; 工艺2:落料—去毛刺—清洗—引深—冲孔—车工
从表2数据可以看出,合理的模具间隙按照工艺1加工零件,零件的一次成品率较高;而且基本上没有反弹;加工效率和大大提高以及投入成本明显较少。
三、装夹方式
装夹方式对车制不锈钢零件至关重要,车制典型动盖板是顶车方式,装夹方式是零件在图5和图6夹具之间(如图7装夹方式),最初车工以图3样的顶板车制零件,受力点是平面,看似相切面多,受力面大,但是新间隙生产出的零件平面度还是不能保证,必须加校平工序才能保证平面度。
经过观察,我们把顶板改成图4形状,让受力点减少,平面大部分悬空,受力面只有2mm,顶板也有斜面(见图5和图6)这样车制零件时候平面度反而得到保证。为此我们经过上万件该零件的实验论证,发现图4的顶板比图3状顶板车制不锈钢零件效果好。
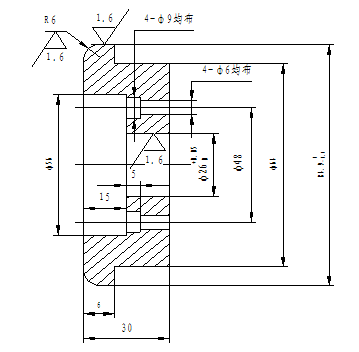
图3
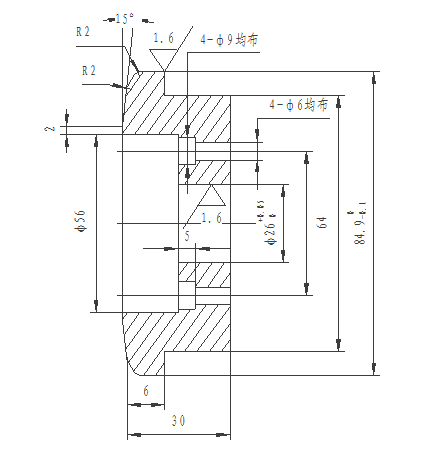
图4
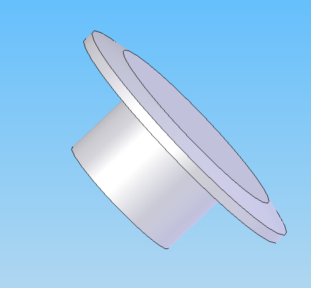
图5 图6
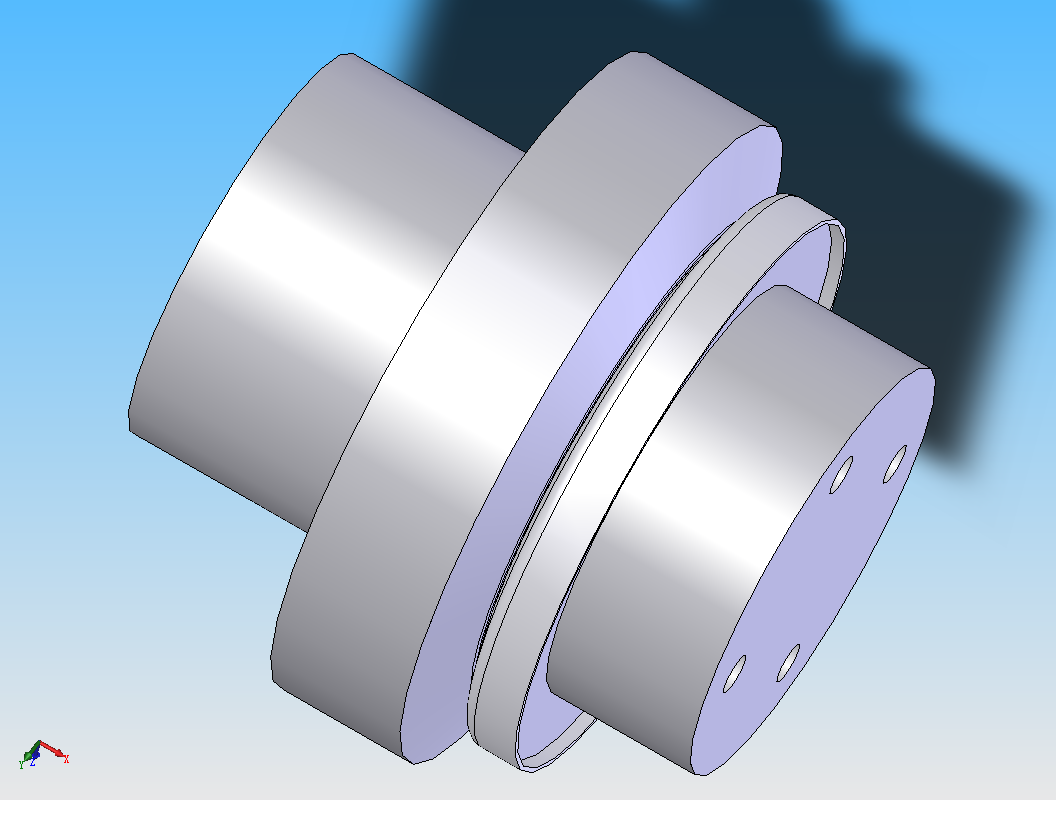
图7
四、结论
新的装夹方式减少零件在装夹过程中破坏零件形状,防止零件车制后回弹,影响零件平面度等问题,新模具间隙在保证零件尺寸与形状的前提下,新夹具尽量少破坏零件原形状这样零件的一次成品率就大大提高。
经过试验结论如下:
1. 不锈钢板料的碾压方向对零件的平面度基本上没有影响。
2. 材料的批号对零件的平面度影响不大。
3. 类似于该零件在模具中保压对平面度及零件的稳定效果不大。
4. 在工艺过程中加退火工序不能解决零件稳定性。
5. 根据板料的实际厚度给出模具的合理间隙为料厚的10%~12%.这样才能保证平面度。
6. 车工的顶板必须配车内孔和斜面。才能保证零件在车制过程中一次车成,达图要求(车制夹具尽量减少零件在装夹过程中破坏零件形状和防止回弹)。
7. 试验证明工艺中有整形工序零件的比没有整形工序零件平面度要好。
8. 取消校平工序,加工效率缩短近1/3。