神龙汽车有限公司 技术中心 王燕萍
摘要 本文介绍了数字化制造技术的基本内涵和工作流程,数字化制造技术在质量控制领域的应用;并对神龙公司工艺领域数字化制造技术的应用现状作了分析,并提出了后续的实施方向和途径。
关键词 数字化工厂 工业化 工艺仿真 PLM 整体规划 尺寸管理
1、概述
从世界范围来看,汽车行业是一个发展成熟、竞争高度激烈的行业,为了获取竞争优势和有利地位,各类创新活动在行业里不断涌现,除了管理创新,各企业更把技术创新当做竞争制胜的利器,数字化技术的开发、应用越来越普遍,在各类产品开发和工艺设计的技术创新活动中承担着不可或缺的作用。数字化技术在工艺领域的综合应用就是数字化工厂技术,目前国内外对此还没有一个统一的概念,一般可以认为数字化工厂技术就是通过计算机虚拟制造技术对生产过程仿真,模拟产品生命周期中的制造、装配、质量控制和检测等各个阶段的功能,主要解决工厂、车间和生产线以及产品的设计到制造实现的转化过程,使设计到生产制造之间的不确定性降低,在数字空间中将生产制造过程压缩和提前,使生产制造过程在数字空间中得以检验,提前解决实际生产中可能出现的问题,并利用计算机技术优化实际生产过程以及整个生产系统的性能,从而提高设计的成功率和可靠性,在最大限度上节约研发的时间和费用。
2、数字化工厂的工作流程及在汽车行业的应用情况
“数字化工厂”系统为汽车制造商及其供应商提供了一个开放的制造工艺信息共享平台,使企业能够对整个制造过程进行设计规划,模拟仿真和管理,并将制造信息及时地与相关部门、供应商共享,从而实现虚拟制造和并行工程,保障生产的顺利进行。
2.1数字化工厂的工作流程(工作流程如图1所示):
2.1.1从设计部门获取产品数据:
通过系统集成,从设计部门的PDM系统中自动下载产品相关数据,包括3D模型、装配关系等;并在“数字化工厂”环境中进行工艺审查、公差分析等,分析产品的可制造性、可达性、可拆卸性和可维护性,实现3D产品数据与3D工艺数据的同步。
2.1.2从工装工具、生产部门获取资源数据(2D/3D):
通过系统集成,从企业的资源库中自动下载相关资源数据;或从供应商取得工装工具的数据,在“数字化工厂”环境中建立相关项目的资源库。
2.1.3 工艺规划:
在“数字化工厂”规划模块中进行协同规划或导入工艺部门已有的工艺信息。产生总工艺设计计划、工艺图表、细节工艺规划,表明工艺与产品、资源的顺序与关联,生成MBOM,规划工厂和车间的流程和工时等工艺信息。
2.1.4 工艺验证、仿真:
将人机工程、机器人、3D设备/工装/夹具、生产线等资源定义并加入到“数字化工厂”工程模块中,构建虚拟的生产环境,仿真工厂作业流程,分析一个完整的数字工厂(车间/流水线)环境,验证规划结果。包括:工艺验证、动态装配、工位布局验证、线平衡、工时分析、人机工程仿真、 工
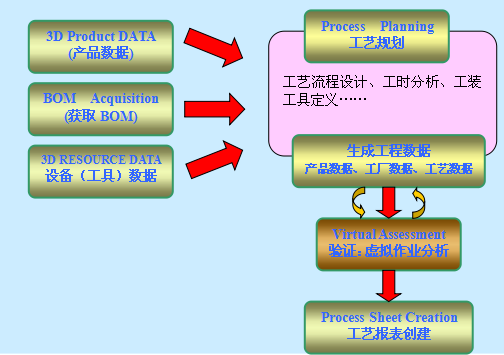
图1 “数字化工厂”工作流程
厂布局、物流仿真、机器人仿真、NC仿真、冲压仿真、PLC仿真和质检等。
2.1.5 客户化输出:
通过系统集成和客户化开发,输出工艺执行文件;输出生产、采购、招投标、维护、培训等信息或将数据传递到现有的CAPP系统中。
2.2 数字化制造技术在汽车行业中的应用
在汽车行业,为提升产品开发质量,加快产品开发速度,并行工程得以大量应用,作为一项先进的并行工程技术,数字化工厂的应用广泛涵盖从产品开发到生产制造的全过程, 如下图所示:
2.2.1冲压解决方案
对冲压生产线进行仿真,可以进行动态力分析、模具体干涉检查、材料流分析,验证工艺设计,在设计阶段就可通图2数字化工厂在汽车制造流 图2 数字化工厂在汽车制造流程中的应用
程中的应用过3D浏览进行更好的信息沟通;可进行早期的设计错误检查 (冲突分析);可方便地进行运动学优化;可同步地进行工艺设计;减少冲压生产线的建立与调整时间并优化工作循环时间。
2.2.2白车身解决方案(焊装)
可以生成、管理和优化整个白车身的工艺流程,提供焊点自动分配、焊枪自动选择、机器人可达性分析、机器人离线编程、生成无干涉焊接路线等工具,实现白车身生产线、装配单元和工艺过程的设计、规划、方案验证及详细的设计和仿真、优化;提供完整的白车身制造工程的规划、设计、管理、项目跟踪的团队协同制造环境,增强了主机厂与生产线供应商的协作,保证信息及时更新、交流和共享。
2.2.3油漆解决方案
对油漆生产线进行仿真,实现油漆生产线和工艺过程的设计、规划、方案验证。提供机器人可达性分析、机器人离线编程、油漆的标准工序等工具,进行动态分析,提供多种统计分析手段:可对多种概率分布(均匀、正态、指数、爱尔朗、经验分布等)进行统计分析,可输出队列曲线图、柱状图、饼状图等,动态图表显示及用户自定义格式,方便优化设计。
2.2.4总装解决方案
图3 机加工生产线规划
总装解决方案主要解决总装生产线的工艺规划:定义装配操作,分配零/部件,定义装配次序;提供对于复杂操作的三维仿真分析,支持生产装配过程分析,可以进行
静/动态干涉分析、工具可达性
分析、装配间隙分析等,人机工程可以进行OWAS工作姿态分析、NIOSH劳动强度分析以及装配可视性分析,通过对人工装配操作的仿真来对操作场地和装配循环时间进行优化等;还可用于多车型同线混装的工艺方案设计和排产计划的制定,具有混产规划过程仿真、分析生产线的性能,包括产量、物流、生产线平衡、瓶颈和缓冲区大小等。
2.2.5发动机及传动系统加工解决方案
对发动机和传动系统加工生产线进行分析、规划和仿真。可以自动识别零件的工艺特征、设计加工工序、自动选择最佳的加工参数和刀具和生成NC刀具路径乃至NC程序,并为生产线上的工位分配优化的工序。
2.2.6工厂设计和优化
可以快速创建精确的3D工厂模型,通过三维实时虚拟现实可视化技术,工厂内的所有设施、生产线、设备等都可以仿真,设计人员可以评估/优化生产线节拍、生产能力、瓶颈、布局、设备利用率和缓冲区大小。
2.2.7质量管理
可以在设计阶段便对公差和装配方法进行优化,并根据定义的质量特征离线地生成供坐标测量机或数控机床使用的测量程序。获得的尺寸信息可与CAD模型对比,分析和优化产品的质量控制。
“数字化工厂”贯穿整个工艺设计、规划、验证、直至车间生产工艺整个制造过程,不是一个独立的系统,需要与设计上游的CAD/PDM系统进行数据交换,对产品设计进行可制造性评审(工艺评审),同时,还需要考虑工厂资源情况,要与下游的企业资源管理系统ERP建立接口。
2.3数字化工厂技术在质量控制中的应用
汽车质量控制的重点之一车身质量往往是整车质量问题的主要来源,而车身质量所设计的内外观性能、钣金链接强度,以及装配难易性也都和制造精度直接相关。而汽车产品的宏观精度(如间隙、面差)和微观精度(如表面光洁度)等的控制很大程度上就是对汽车各种尺寸的控制,所以汽车质量控制的关键是有效地进行尺寸偏差控制和管理。
通常的乘用车仅车身装配就设计300~500个薄板冲压零件,150~250个夹具,70~120个装配站,2000~6000个焊点,再加上内外饰件,整个制造装配过程长而复杂,而诸多尺寸的偏差在这个过程中不断地传递和积累。因此对尺寸偏差的控制和管理需要贯穿汽车质量控制的全过程。
在产品设计阶段,数字化工厂技术依靠仿真分析工具进行虚拟原型模拟,考虑和解决后续的制造问题,对设计和工艺进行优化,这种设计方法就叫做产品保质设计(Design for Quality),通过3D的尺寸链仿真分析工具,仿真产品的制造和装配过程来预测产品尺寸质量和偏差源贡献因子,从而判断某一阶段的设计是否能够满足尺寸设计要求并给出可能的整改方案。
在加工制造阶段,用数字化的方式来设置、仿真、和运行CMM(Coordinate Measuring Machines,三坐标测量仪)和CNC(Computer Numerical Control Machine,数控加工设备,实现离线编程和在线检测。在现生产阶段,从工厂各类测量设备里获取质量数据,实时获取生产质量信息,对此进行跟踪、分析和发布。通过检测数据的深度关联分析寻求问题的根本解决方案,从而提高产品的最终质量,同时提高生产效率并降低生产成本。
3. DPCA制造领域数字化技术应用的现状及分析
目前,在神龙公司产品部门使用数字化设计工具(如CATIA,ALIAS)进行设计工作已经非常普遍,用R3P系统管理设计流程和设计数据也已经应用了4年,计算机辅助工程(CAE)的技术已开始在产品设计中得到逐步应用,这些产品设计领域的数字化应用也要求下游工艺部门对其工作模式和工作方法进行变革,需要工艺部门在没有实物之前就依据数字化定义开展产品的工艺可行性分析和验证,为产品开发提供优化意见和建议,从而实现产品工艺同步。从工具层面来看,神龙公司数字化工具应用在局部已开始起步,但应用的范围和深度均非常有限,具体表现在:
3D尺寸链计算分析,2010年引进了3D尺寸链计算分析软件3DCS,在Tx3内饰件定位尺寸链核算中得到应用。在新车型项目T88项目中应用该软件,计算了尾门装配、尾灯与尾门间隙面差、前门护板与侧围护板安装孔位等尺寸分析。并且在现生产车型T73中试行应用该软件,重点关注缺陷集中的尺寸。
装配评审(又称ECM),新车型专用零件的装配评审原来该工作由PSA完成初始工作,总装工艺进行校验。从T73项目开始装配评审都是由DPCA的总装工艺完成的,在装配评审的过程中,需要将零件、设备、工具的信息进行3D数字化,然后进行模拟装配,以提前发现装配干涉或者其他问题,最终得出报告,供项目组评估。现在只能利用CATIA V5 的DMU模块进行简单的装配模拟、工具通过性模拟分析干涉,分析效率低,而且对于空间间隙较小,型面复杂零件,很难达到效果,但如果使用一些分析工具,如达索公司的数字化制造解决方案DELMIA中的Kineo插件(装配路径的自动计算);西门子公司的Teamcenter Visualization Mockup可视化数字样机可以方便高效地进行间隙和干涉分析,这样不仅可以帮助工艺人员提高设计验证工作的效率,而且可以在工艺的验证和优化方面投入更多精力,进一步改善工作质量。
3D数据浏览: 要实现产品工艺设计同步,对工艺部门而言,在制作工艺的时候,首先就需要一个图形工具来浏览3D数模,了解产品的信息,才能进行工艺设计。目前公司采用了Inte Vue产品,和工艺数据管理平台集成在一起。该工具对CATIA的产品数模轻量化,并能浏览轻量化数模,可以进行简单的批注说明,转化为工艺附图去指导操作。
工艺规划:利用3D数模来进行工艺规划,进行数字化验证和模拟工作,由于缺乏工具,基本上是依赖供应商或PSA来完成,但是DPCA已在某些领域开始尝试。例如:焊装工艺于T53新车型项目开始已要求集成商在交付实物前做虚拟验证,提供3D文件,已积累了T63、B53、T61、B51、T31、T31、X7等车型主线3D的基础数据。总装工艺从2008年开始应用物流仿真模拟软件,用该软件建立了二厂总装生产线输送设计方案的建模和仿真模拟,验证了输送方案的合理性,找出物流的瓶颈点,并利用所得到的结果对输送方案进行优化布置。
从工艺数据管理层面来看,2011年启动了PDS(Process date System,工艺数据管理)项目,自行设计开发实施神龙公司的工艺数据管理平台,管理冲压、焊装、油漆、总装、机加五大工艺从生产准备到现生产的工艺过程中的工艺数据,包括零件、操作、设备、工具、工时、图形等信息。
总之,神龙公司在工艺领域的数字化应用起步较晚,只实施了一些独立的解决方案,无论是工艺数据管理方式还是工艺设计模式,与行业先进水平相比均有较明显的距离,需要采取切实的行动加以改善。
5.结束语
目前应该是神龙公司在制造领域实施数字化技术的恰当时机:
图4 PDS系统总体设计
– 契合行业发展的趋势,从2009年开始中国汽车市场高速增长,进入行业发展的高峰期,公司的新项目、新车型投放越来越多,越早实施可以越早受益;
– 已具备实施的基础条件
---在外部,数字化工厂产品、技术已比较成熟,各大汽车厂商都在陆续应用,有经验可供借鉴;
---在内部,本公司的信息化程度整体比较高,在产品设计领域CAD 和 R3P系统的应用已运行多年,MBOM(制造明细表)的管理很成熟,工艺部门已经积累一些3D数据,并积累了一定的系统实施和应用经验。
工欲善其事,必先利其器。就像在产品领域应用CAD、CAE技术,生产领域应用ERP技术,工艺领域数字化技术的应用也会带来技术革新和管理上台阶,从而提升公司的竞争能力,抢占行业的制高点。
参考文献
1.《数字化企业》 2009金秋版
2.《剧变时代中国卓越汽车企业的创新之道》