李 硕(北车兰州机车有限责任公司质量保证部理化室)
摘要: 采用化学分析、断口分析、金相分析等方法,对某厂断裂的热作模具进行分析,结果表明:该模具的断裂时由于原材料带状组织严重,在正常的热处理工艺下,造成严重的组织不均匀及残余应力较大,因而在使用初期就发生断裂。
关键词: 模具;5CrMnMo钢;断裂;淬火;残余应力
1 情况简介
某机车公司锻工车间委外制作的一批5CrMnMo热锻模具在使用初期就出现裂纹,裂纹基本贯通,只有内部一小部分相连,如图1所示。模具材质为5CrMnMo,尺寸为300mm×500mm×700mm,该模具的加工工艺为:下料 锻造 退火 粗加工 热处理 精加工。技术要求硬度为HB364-415。
.jpg)
图1 断裂模具宏观形貌
2理化检验
2.1断口检验
带裂纹的模具经铁锤轻击断裂为两部分,断面如图2照片所示,可见裂纹起源于近表面,有轻微向四周的放射线,基本贯通,断口平齐,没有明显的塑性变形。
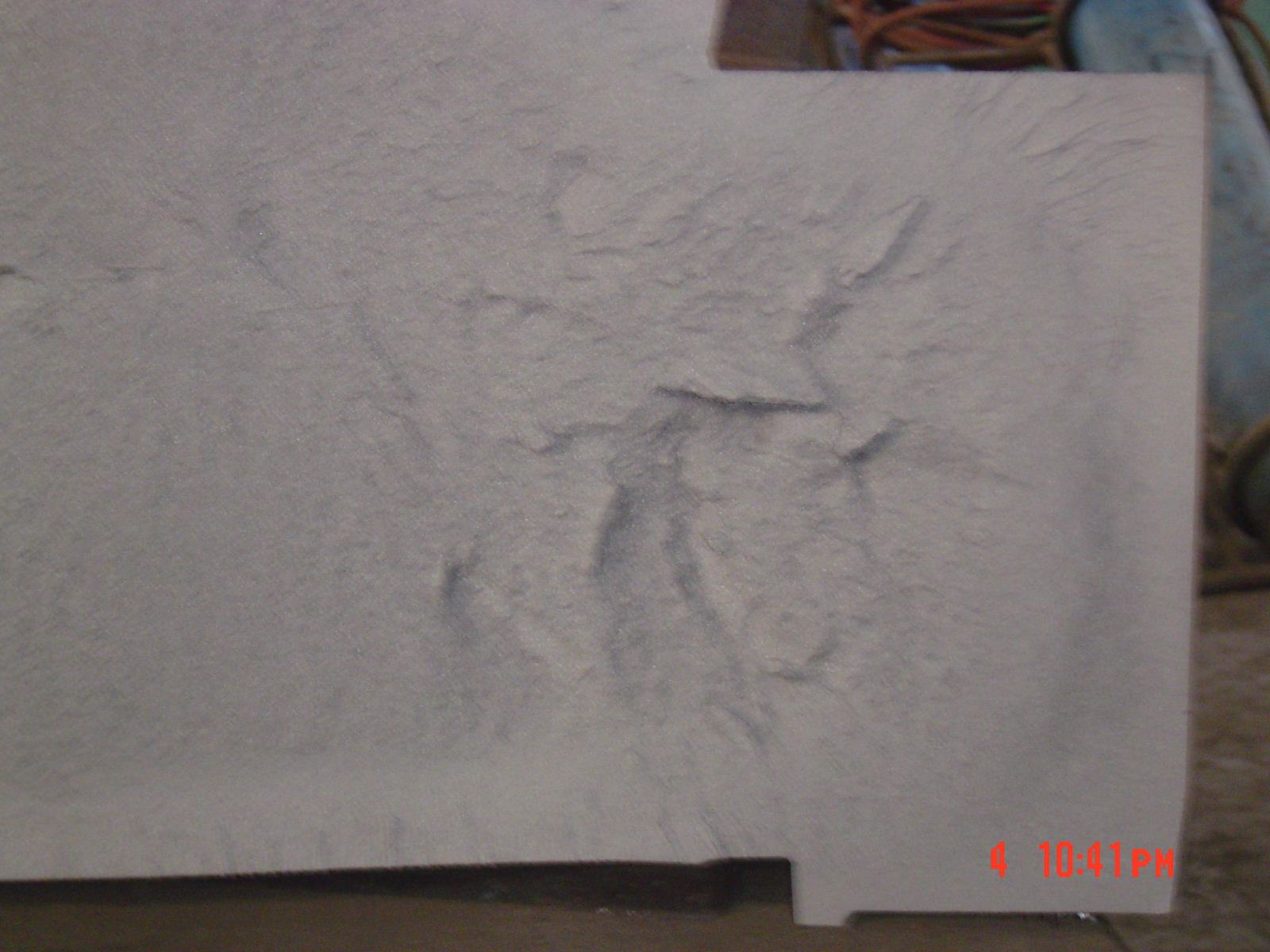
图2 模具断口宏观形貌
2.2化学成分分析
在裂纹附近取样,对模具材料成分进行化学分析,结果如表1,表明,材质符合GB1299--85《合金工具钢技术条件》中5CrMnMo的要求。
表1化学成分分析结果(质量分数)
%
元素
|
C
|
Si
|
Mn
|
Cr
|
Mo
|
P
|
S
|
实测值
|
0.56
|
0.47
|
1.41
|
0.74
|
0.22
|
0.013
|
0.018
|
标准值
|
0.50-0.60
|
0.25-0.60
|
1.20-1.60
|
0.60-0.90
|
0.15-0.30
|
≤0.030
|
≤0.030
|
2.3金相检验
我们利用DK7725型线切割机在裂纹附近切取金相试样,经过磨抛后,在Neophot32金相显微镜下观察,根据GB/T10561—2005检验非金属夹杂物,按A法评定结果为A1,B1,C0.5,D1,虽然GB1299—85 未对非金属夹杂物做硬性规定,但是,可见夹杂物含量不高。
试样经4%(体积分数)硝酸酒精溶液侵蚀后,在50×显微镜下观察,其显微组织如图3所示,可见带状组织十分严重,在400×显微镜下观察,偏析带中基体组织为及回火马氏体,回火马氏体呈带状偏析,马氏体针长4级。如图4所示。而非偏析带的组织主要是回火托氏体如图5
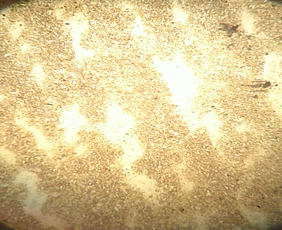
图3 模具断口处显微组织
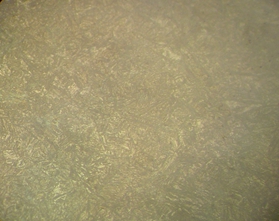
图4 偏析带的显微组织
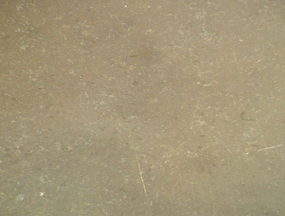
图5 非偏析带的显微组织
2.4 硬度检验
按照GB/T231.1--2002分别在模具表面和裂纹源处进行布氏硬度测试,结果见表2,可见基本符合技术要求。
表2 硬度测试结果
试样位置
|
裂纹源处
|
模具表面
|
硬度值
|
395,388,391
|
399,402,397
|
3 分析讨论
热作模具的工作特点是在一定的负荷下,使炽热的固体金属产生一定的塑性变形,5CrMnMo是传统的热作模具钢,韧性高而热强性较差,供货状态的5CrMnMo存在这一定的带状组织,即合金元素偏析带,[1]因此锻造时必须反复镦粗和拔长,尽量消除带状组织,使组织均匀化。
失效的模具断口表明是典型的脆性断口,理化检验表明该模具的化学成分、非金属夹杂物及硬度都符合要求,显微组织分析表明带状组织严重,这是该钢种常见的一种缺陷组织,该钢淬火回火后的理想组织是均匀细小的托氏体,而该模具由于合金元素偏析而造成淬火后组织中有较多的马氏体,加大了脆性,[2]这样的带状组织在淬火时产生较大的附加组织应力,[3]同时富含合金元素的部位由于回火稳定性大,在正常的回火工艺下,组织应力得不到充分消除,造成较大的残余应力。我们知道,钢在淬火时,主要产生组织应力和热应力,组织应力最终的结果是使表面产生拉应力,而热应力最终使钢表面产生压应力,而尺寸不大的工件一般组织应力起主要作用,[4]因而工件表面呈残余拉应力状态,同时组织中马氏体脆性大及组织不均匀和附加组织应力加剧了这种作用,因而在使用初期就发生断裂。
4 结论和建议
通过以上分析可见,该模具钢原材料带状组织严重,而在锻造时又未能消除这些带状组织,在正常的热处理工艺下造成残余应力较大,因而在使用初期就发生断裂。
建议加强原材料检验,不用不符合要求的原材料;通过反复锻造,并且采用完全退火的工艺,尽量消除带状组织,使组织均匀化;可以采用资料[5]中介绍的新的热处理工艺。
参考文献:
[1] 蔡美良,丁惠麟,孟沪龙.新编工模具钢金相热处理[M].北京:机械工业出版社,1998.140.
[2] 李炯辉主编.金属材料金相图谱[M].北京:机械工业出版社,2007.830.
[3] 蔡美良,丁惠麟,孟沪龙.新编工模具钢金相热处理[M].北京:机械工业出版社,1998.144.
[4] 易文质.模具热处理[M].湖南:湖南科学技术出版社,1981:251.
[5] 杨金花.5CrMnMo钢制热锻模热处理工艺改进[J].金属热处理,2007(11):99-100.
5CrMnMo模具断裂分析
北车兰州机车有限责任公司质保部理化室
李硕
二零零一年八月三日