吕凤军, 傅国如,陈荣,李权
(北京航空工程技术研究中心,北京 100076)
摘要:本文对某型故障齿轮损伤痕迹、断口形貌、齿轮材料成分、组织、硬度和渗碳层厚度进行了检查与分析。分析结果表明:断齿的断裂性质为弯曲疲劳断裂,在齿轮运转过程中非正常啮合以及齿根部位的加工刀痕处形成的较大的应力集中是导致疲劳裂纹萌生的主要原因。
关键词:锥齿轮;断裂;弯曲疲劳
中图分类号:TG157 文献标识码:A
Tooth Fracture Analysis of aero-engine bevel gear
LV Feng-jun, FU Guo-ru, CHEN Rong, LI Quan
(Beijing Aeronautical Technology Research Center, Beijing 100076 China)
Abstract: In order to investigate the reason for the tooth fracture failure of bevel gear, the means, such as fracture observation, X-ray energy spectrum analysis, microstructure, carburized layer and hardness examinations, were carried out. The results showed that the tooth fractured due to bending fatigue, the abnormal mesh in the running course of bevel gear and stress concentration in the gear foot caused by rough machining trace were the main reason for the tooth fracture failure.
Key words: bevel gear; fracture; bending fatigue
传动齿轮是传递功率和运动的重要部件,由于工作条件非常复杂,在不同条件下使用会造成不同的失效的特征,其失效形式往往表现为齿面点蚀、胶合、磨损、塑性变形和齿轮断裂[1-4]。齿轮断齿为常见故障,但每次故障特征会存在较大的差异,为此,本文对某型发动机锥齿轮的断齿特征检查与分析,最后给出了断齿原因。
故障锥齿轮的材料牌号为12Cr2Ni4A,齿型面和齿根渗碳深度为0.7~1.1mm,渗碳表面硬度大于60HRC,非渗碳区硬度32~45.5HRC;截止检查发现断齿时,垂直被动锥齿轮的总使用时间2800小时。
1 外观检查
故障锥齿轮如图1所示,该锥齿轮为垂直被动齿轮,工作旋转方向应为顺时针方向(按图1中视角),断齿的断裂位置位于齿根倒角与齿面交接部位。
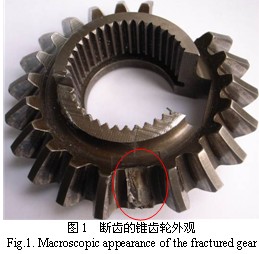
在未断裂的所有齿的凹面和凸面上,均有明显的啮合磨损痕迹。除与断齿前后相邻的两个齿外,其它齿的磨损位置及其损伤程度基本一致,已充满整个齿长,磨损最严重的位置已偏离齿面节线,均位于磨损痕迹内侧边缘,齿面上已出现麻点,凸面相对较多。与断齿相邻的前一个齿的凹面磨损严重,在该齿的节线偏下部位有一个凹槽状磨损痕迹,宽度约为4.4mm,凹槽边缘有多处明显的表层疲劳剥落,见图2。与断齿相邻的后一个齿的凹面磨损偏靠齿顶部位,靠近大端面的齿顶宽度明显变小,在该齿节线的中部有多处明显的表层疲劳剥落,见图3。
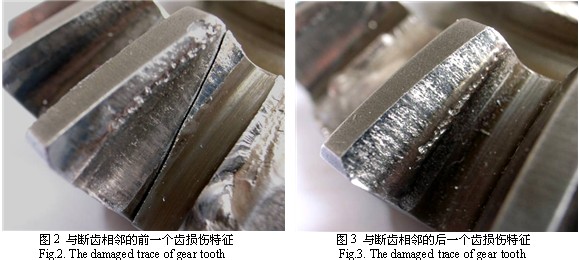
宏观观察,断口呈凹形,具有典型的宏观疲劳断裂特征,疲劳裂纹起始于靠近锥齿轮内侧齿根倒角与齿面交接部位的表面,见图4。疲劳扩展区断口较细腻,呈光滑陶瓷状形貌特征,可见清晰的贝壳状花样。最后瞬裂区表面较粗糙,有明显的约呈45?剪切唇特征。
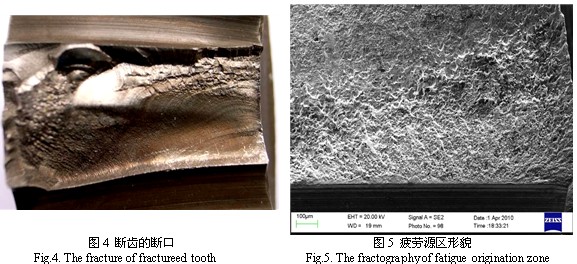
微观观察,疲劳源区有清晰的放射棱线,源区侧面有明显的机械加工刀痕,疲劳裂纹从刀痕处萌生,未发现冶金缺陷、腐蚀和外物损伤等痕迹,见图5。齿面中部的断口边缘有多处表层疲劳剥落,见图6,疲劳剥落区处在齿根倒角与齿面交接部位的表面,且远离疲劳源位置,该部位不存在表面接触,可以判定,疲劳剥落不是表层接触疲劳剥落,而是在断齿的疲劳裂纹萌生之后、裂纹两端张口不断挤压闭合造成的。最后瞬裂区形貌特征为韧窝,见图7。
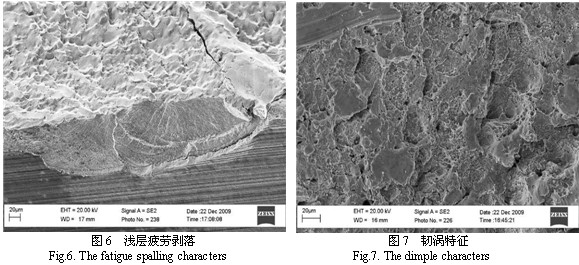
3 材质检查
3.1 成分检查
对断口表面进行X射线能谱成分分析,其成分和含量与12Cr2Ni4A基本相符,结果见表1。
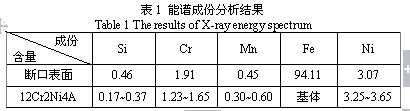
成份 含量SiCrMnFeNi
断口表面0.461.910.4594.113.07
12Cr2Ni4A0.17~0.371.23~1.650.30~0.60基体3.25~3.65
3.2 渗炭层检查
切取一个未断裂齿的剖面(与齿面垂直的截面),做成金相试样,用4%硝酸酒精溶液腐蚀后观察,齿剖面上不同部位的渗碳层厚度基本相等;从显微硬度值随渗碳层深度的变化关系来判断,渗碳层深度约为0.90mm,满足设计要求的渗碳层深度0.7mm~1.1mm,见图8.
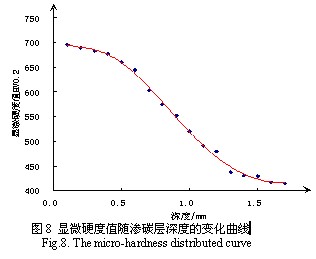
3.3 组织和硬度检查
渗碳层为马氏体+断续分布的细小碳化物混合组织,见图9,心部为马氏体和少量铁素体混合组织,见图10,组织均属正常。
对齿表面和心部进行洛氏硬度检查,结果见表2。齿面和心部的洛氏硬度均符合设计要求。
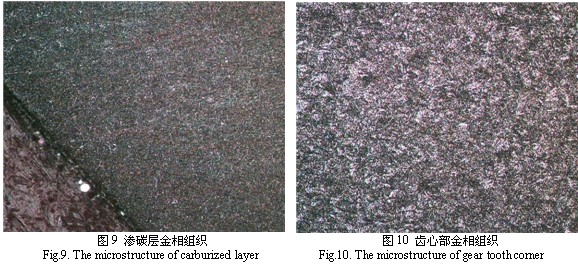
表2 洛氏硬度测量结果
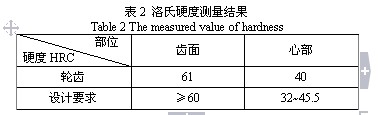
部位 硬度HRC 齿面心部
轮齿6140
设计要求≥6032~45.5
4 分析讨论
断齿的断口具有线性疲劳源,疲劳裂纹起源于靠近锥齿轮内侧齿根倒角与齿面交接部位的表面,疲劳扩展区有清晰的疲劳弧线和疲劳条带特征,由此表明,垂直被动锥齿轮断齿的断裂性质为弯曲疲劳断裂。
与断齿前后相邻的两个齿磨损严重,但这两个齿的磨损位置与断齿的断裂位置明显不同,没有直接的对应关系,说明这两个齿的不正常磨损是在断齿后形成的。
齿面中部的断口边缘有多处表层疲劳剥落,该部位位于齿根倒角与齿面交接部位,不存在齿面间的表面接触,在齿轮正常工作情况下,不可能产生表层接触疲劳剥落,这些特征说明表层疲劳剥落产生于疲劳裂纹萌生之后,是疲劳裂纹两端张口不断挤压闭合导致的表层疲劳掉块。在未断裂的所有齿的凹面和凸面上,均有明显的啮合磨损痕迹,损伤最严重的位置偏离齿面节线,均位于磨损痕迹内侧边缘,这些特征充分表明垂直被动锥齿轮出现了不正常啮合,不正常啮合是导致断齿的主要原因。疲劳源区侧面有明显的机械加工刀痕,疲劳裂纹从刀痕处萌生,说明加工刀痕对疲劳裂纹的萌生有一定的影响作用。
锥齿轮的成分、组织、硬度和渗碳层深度均符合设计要求,说明锥齿轮材质正常。
5 结论
1)锥齿轮断齿的断裂性质为弯曲疲劳断裂,疲劳裂纹起源于锥齿轮内侧齿根倒角与齿面交接部位的表面。
2)垂直被动锥齿轮在工作中出现不正常啮合,是导致断齿的主要原因。
3)垂直被动锥齿轮材料成分、组织、渗碳层和硬度均符合要求,疲劳断裂与齿轮材质无关。
参 考 文 献
[1]中国机械工程学会材料学会.疲劳失效分析[M].机械工程出版社,1987.
[2]陶春虎,钟培道,王仁智.航空发动机转动部件的失效与预防[M].北京:国防工业出版社,2000.
[3]王新社.齿轮轴失效分析[J ].金属热处理,2002,27(9):54-56.
[4]张卫方,赵爱国,刘高远,李运菊,陶春虎.某尾减齿轮齿面损伤与断齿分析[J].机械工程材料,2003,27(8):47-50.