某化工厂一台二氧化碳压缩机在连续工作时发生曲轴突然断裂事故。该曲轴材料为45钢,处理过程为锻造后正火。为了查清曲轴断裂的真正原因,笔者受委托对该断裂的曲轴从宏观断口形貌、化学成分、力学性能、超声波探伤及显微组织等方面对其失效原因进行了分析。
1 试验结果与分析
1.1 宏观断口分析
断裂位置发生在曲轴的曲拐径上,其断口大部分垂直于曲拐径轴线,且中间凹,周围凸,中间部位有金属光泽,整个断口没有明显的宏观塑性变形。最终瞬断区与曲拐径轴线大约成30°角,长约250 mm;表面粗糙,并伴有明显的点状金属光泽,其投影面积约占断口面积的1/7;在曲拐臂与曲拐径过渡处发现有金属疲劳源,且有向内扩展的贝壳状疲劳延伸线,由此可以看出该曲拐属于疲劳断裂(见图1)。另外,由瞬断区所占比例可以看出该曲轴所受应力集中程度不是很大,说明在设计上没有问题。
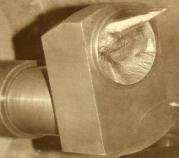
图1 曲轴宏观断口形貌
Fig.1 Fracture macrograph of the crank shaft
1.2 化学成分检验
在断裂处取样进行化学成分检验,结果见表1。显然,其化学成分符合45钢要求。故应排除由于材料成分不符合要求而造成断裂这一因素。
1.3 力学性能测试
在曲拐径靠近断口处取试样,沿纵向切取,其横截面为1/3R处,制成标准试棒后,在WE-30型液压式万能材料试验机上测试,其结果如表2所示。由表2可知,其屈服强度、冲击性能及硬度均小于要求的标准值,说明其抗拉强度、冲击韧度、硬度均不能满足设计要求。
表1 曲轴化学成分(质量分数,%)
.jpg)
1.4 超声波探伤
用直接接触法对该曲轴进行超探,发现在曲拐臂、曲拐径处存有缺陷,缺陷反射量相当Φ2~Φ3平底面当量,埋藏深度距曲拐臂一侧表面60~170 mm之间,并构成缺陷密集,其缺陷密集区占检测总面积的百分比已超出JB/T 6908—2006《容积式压缩机用钢锻件》标准所规定的要求;同时在探伤过程中还发现该曲轴伴有声衰减严重现象,甚至还出现过一次底波不满饱合的现象,说明该曲轴组织存在严重粗晶。
1.5 显微组织分析
试样取自距断口30 mm的曲拐径处,用4%硝酸酒精侵蚀后,在光学显微镜下观察,发现组织异常粗大,晶粒度大于1级,基体为珠光体加沿晶界析出并向晶粒内扩展的针状铁素体,且伴有较为明显的魏氏组织,魏氏组织达4级(见图2)。晶粒粗大和魏氏组织都是金属过热的产物。魏氏组织是亚共析钢中,由于加热温度过高,保温时间过长(即发生过热现象)使钢的奥氏体晶粒粗大,加之在A3→A1温度区间冷却速度较快,铁素体不能充分沿奥氏体晶界析出,而是在过饱和的奥氏体晶粒内沿一定的晶面上析出,并与旧相奥氏体保持一定结晶位向关系的先共析铁素体或渗碳体。晶粒粗大及魏氏组织出现后,钢的韧性显著降低,脆性增加。
.jpg)
图2 曲轴试样的显微组织 ×100
Fig.2 Microstructure of the crank shaft ×100
2 结论与建议
依据以上结果,该曲轴断裂失效的原因如下:
1) 由于热加工不当,该曲轴基本组织呈过热形态,没有得到应有的片层间距较小的珠光体组织,却出现了晶粒粗大和较为明显的魏氏组织,这些非正常组织大大降低了钢的塑性和冲击韧性,直接削弱了曲轴的力学性能,使之达不到设计时的要求,在交变载荷作用下,极易诱发金属疲劳,造成早期失效。这是曲轴断裂的主要原因。
2) 由于正火后,没能消除锻造中产生的过热缺陷(晶粒粗大及伴有魏氏组织),也没有达到细化组织的效果,说明正火过程是失败的,没能按正确的正火工艺操作,这是曲轴断裂的另一原因。
鉴于以上因素,特提出以下改进建议:
1) 钢在冶炼、热扎时要严格按照工艺要求去操作,要充分脱氧,并控制好加热温度和冷却速度,以避免出现晶粒粗大和魏氏组织。
2) 合理选择锻造比。锻造加工可以矫正晶粒粗大、魏氏组织等缺陷,但是锻造比不合适时,往往达不到预期的效果。根据钢锭锻造比与力学性能的关系,对45钢应取锻造比2~3。
3) 在曲轴正火处理时,要严格控制加热温度、保温时间,通过正确的热处理工艺[1],以得到片层间距较小的珠光体组织,确保曲轴具有良好的综合力学性能。
4) 如有可能,可进行调质处理,这样会提高曲轴的力学性能。
后与委托方、加工方沟通,按上述建议重新制造一根曲轴,经检验各项指标合格,至今在委托方使用良好。
参考文献:
[1] 卢银德. 大型锻件的热处理工艺[J]. 金属热处理, 2004, 29(4): 47-49.
[2] 庄 森, 卢银德, 文立刚. 螺杆钻具传动轴断裂分析[J].金属热处理, 2005, 30(6): 88-89.
作者:庄森