(中国北车兰州机车有限责任公司质量保证部,兰州730050)
李硕
摘要:某内燃机车牵引电机转轴发生断裂,利用断口分析、低倍检验、金相分析、化学成分分析、力学性能分析等对断裂的电机转轴进行分析,结果表明,由于堆焊修复过程中,堆焊电流过大,造成的化学成分偏析,以致在冷却过程中造成条带状分布的铁素体,致使疲劳性能下降,在循环应力的作用下造成的早期高周疲劳断裂。
关键词:电机转轴;绿色制造;失效分析;疲劳;堆焊;再制造;
1.情况简介
某机车公司检修的内燃机车,在出厂不到半年的时间,发生牵引电机转轴断裂,经拆卸检查,牵引电机转轴完全断裂,轴承箱顶部破裂,轴承箱内无缺油现象。电机其他部分完好。电机转轴断裂于R圆弧处,电机返厂后拆下的断裂的电机轴见图1。
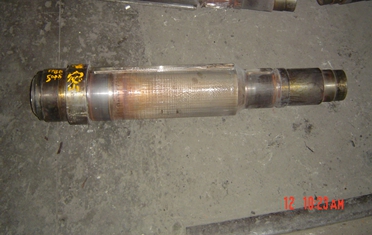
图1
电机转轴的材质为35CrMo,制造工艺为:下料 锻造 正火 调质 机械加工 探伤。经调查,该电机轴在厂修时曾进行堆焊修复,堆焊修复的工艺为:在电机转轴待修复部位进行切割打磨,除去待修复部分铁锈、油、水分及氧化皮等,将焊条在360℃烘干1小时,焊前对待修复部位进行适当加热,采用直流反接进行堆焊,堆焊后分别进行VT、UT及MT检查,焊条为结607焊条,是低氢钠型药皮的低合金高强度焊条,符合GB E6015—D1要求。
笔者对断裂的电机转轴进行了检验分析。
2.理化检验
2.1断口检验
该电机转轴断口平齐,无明显的宏观塑性变形,断口上有十分明显的疲劳贝纹线,并且具有贝纹线的疲劳裂纹扩展区占据较大的面积,断口边缘呈棘轮状,为典型的扭转及弯曲多源疲劳断口,表明电机转轴的断裂属于疲劳断裂,裂纹起源于轴的表面,断口如图2.
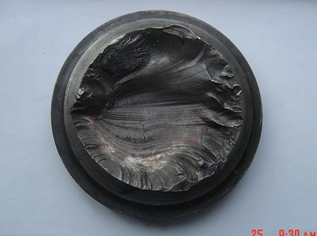
图2
2.2化学分析
在断口附近1/2R处,按规定取样,进行化学分析,结果如表1.分析结果表明,材料成分符合GB/T3077--1999对35CrMo的规定。
表1化学成分分析结果(质量分数) %
元素
|
C%
|
Si%
|
Mn%
|
P%
|
S%
|
Cu%
|
Cr%
|
Mo%
|
检测值
|
0.34
|
0.27
|
0.55
|
0.013
|
0.017
|
0.067
|
0.94
|
0.18
|
标准要求
|
0.32-0.40
|
0.17-0.37
|
0.40-0.70
|
0.035
|
0.035
|
≤0.20
|
0.80-1.00
|
0.15-0.25
|
2.3力学性能检验
按规定取样进行力学性能的检验。按照GB228—2002进行拉伸试验,按照GB229—2007进行冲击试验。结果如表2。
表2 拉伸试验结果
|
抗拉强度
Rm(N/mm2)
|
屈服强度
Re(N/mm2)
|
断后伸长率
A(%)
|
冲击韧性
ak(J/mm2)
|
检测值
|
755
|
570
|
18
|
83
|
技术要求
|
≥735
|
≥540
|
≥15
|
≥58.9
|
结果表明,力学性能符合电机转轴的技术要求。
2.4低倍检验
按照GB226-91进行低倍检验,结果如表3。
表3 电机轴低倍检验结果
|
一般疏松
|
中心疏松
|
锭型偏析
|
一般点状偏析
|
边缘点状偏析
|
检测值
|
1
|
0.5
|
1
|
0
|
0
|
技术要求
|
≤3
|
≤3
|
≤3
|
≤1
|
≤1
|
结果表明,低倍符合GB/T3077--1999的要求。
2.5金相检验
采用DK7725型线切割机在断口附近切取金相试样,经磨光,利用金刚石喷雾剂进行抛光,按照GB10561--2005进行夹杂物的检验,检验结果为 :A1,B1,C1,D0.5,试样经4%硝酸酒精溶液侵蚀后在400倍显微镜下观察,轴表面组织为索氏体,如图3,心部组织为索氏体+铁素体,如图4;对堆焊层分别在40倍,100倍和400倍显微镜下观察,结果如图5、图6、图7。由检验结果可见电机转轴表面和心部组织正常,基体和堆焊层之间熔合线附近无明显焊接缺欠,堆焊层组织主要为索氏体,但是沿着轴的径向,有呈条带状分布的铁素体,铁素体形状为针条状及块状。
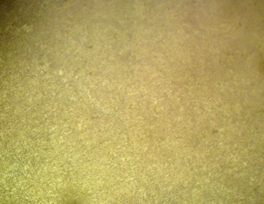
图3 电机轴表面组织 400×
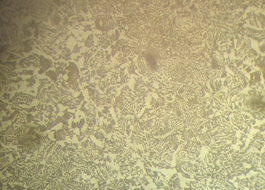
图4 电机轴心部组织 400×
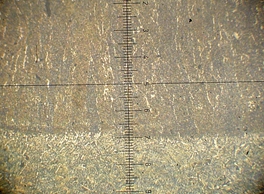
图5堆焊层与基体间的熔合线 40×
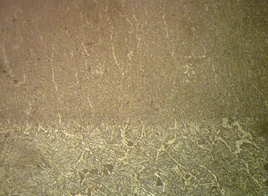
图6 熔合线两侧组织 100×
.jpg)
图7 堆焊层中的条状铁素体400×
3.分析讨论
由检验结果可以看出,该电机转轴的化学成分、力学性能、低倍及金相组织均符合标准及图纸要求。
由堆焊部分的金相检验结果可知,焊缝无明显的缺欠,热影响区组织无明显异常,但是在堆焊层中有沿轴径向分布的铁素体条带,在400倍下可以看到铁素体的形状为针状和块状,考虑到堆焊工艺的特点,这是由于成分不均匀,在冷却时的温度梯度的影响下造成的,而堆焊成分及组织不均匀,主要是堆焊电流过大造成的组织偏析[1],铁素体硬度较低,尤其是针状铁素体强度和韧性均差,针对高周疲劳而言,材料的强度水平越高,疲劳极限越高[2],强度越低,则疲劳极限也越低,并且铁素体与周围其他组织的变形不一致,易在相界面产生裂纹等缺陷。电机转轴在运行中主要承受扭转力矩和弯曲力矩[3],且轴表面的应力是最大的,当组织中存在较多条状铁素体时,在循环应力的作用下,于轴表面很快萌生了疲劳裂纹,在运行中应力的持续作用下,裂纹不断扩展,达到临界尺寸,最终失稳扩展,导致断裂。
发生电机转轴断裂事故后,厂家已经停止了对电机转轴的堆焊修复,笔者认为这是不合理的,因为在机车修理中,零件修复工作十分重要,尤其在零件供应紧张,库存较少或零库存,并且机车检修周期短的情况下,更加体现出零件修复的必要性。从经济及生产成本考虑,一般情况下,制造一吨新零件大约需要3~5吨的原材料,而修复一吨零件只需数十公斤到数百公斤原材料,对钢质零件的堆焊修复在机车修理工作很重要,修复零件的成本仅为新零件的10~14%,能够花费较小的代价取得重大的经济效益,并且一般情况下,堆焊修复后的零件性能不但不会低于原来的性能,而且由于各种堆焊技术的发展,新技术及工艺的采用,修复后的零件的性能还会大大超过新造产品的性能[4]。除此以外,从环保方面看,零件制造从采矿、冶炼、锻造到热处理、机加工等各个环节都要消耗大量的能源,并且,造成较大的污染物排放,对环境影响较大。我们认为,只要严格执行堆焊工艺,就可以避免偏析造成的组织不均。或者略微增加焊条的碳含量,不仅有助于减少铁素体的产生,而且可以增加转轴表面的强度,而增加表面强度有助于提高高周疲劳性能,还可以采用等离子堆焊、激光熔覆等先进技术进行修复;国外在上世纪就进行了很多此类轴堆焊修复的研究工作[5][6],国内也进行了大量的堆焊修复工艺研究,尤其在电机转轴的堆焊修复中研究较多[7]~[10],因此此类转轴的堆焊修复工艺至今已经是较为成熟的工艺。
4.结论及建议
该电机转轴的断裂是由于堆焊修复过程中,堆焊电流过大,造成化学成分的偏析,因而在冷却过程中造成沿轴径向呈条带状分布的铁素体,致使疲劳性能下降,在机车运行中,循环应力的作用下造成的早期高周疲劳断裂。
建议,严格执行堆焊修复工艺;或者改进堆焊工艺,采用强度高的焊条;或者采用等离子、激光熔覆等先进的堆焊修复工艺。
堆焊等零件修复,是符合现代再制造理念及先进的“绿色制造”新概念的先进制造工艺[11],无论从缩短机车检修周期,降低机车检修成本,还是从节能减排等方面都有较大的优势,并且经过修复的零件的性能一般要超过新制造的零件,而且,研究表明,反复堆焊修复对零件基体的组织和性能影响很小,可以多次修复[12]。目前,国家自然科学基金、国家863及973工程研究项目中都已经将再制造工程及其失效分析列为研究课题。因此作为企业,应大力开展零件修复工作,开展修复工艺、修复零件检查工艺及修复零件失效分析的研究等相关工作。
参考文献
[1] 王娟,陈茂爱,孙俊生,等.表面堆焊与热喷涂技术[M].北京:化学工业出版社,2004:100.
[2] 陈南平,顾守仁,沈万慈.失效分析[M].北京:清华大学出版社,1998:80.
[3] 杨黎明.机械原理及机械零件(下册)[M].上海:高等教育出版社,1983:208.
[4] 李亚江,张永喜,王娟,等.焊接修复技术[M].北京:化学工业出版社,2005:2.
[5] Ю.А.Коновалов.用硬质镀铁修复发电机电枢轴磨损配合面[J].国外机车车辆工艺.1984.1:19-24.
[6] Н.И.Бойко.用耐磨材料堆焊并同时进行机加工的方法修复零件.[J].国外机车车辆工艺.1984.6:35-37.
[7] 刘和平.宋占煌.周世玲.1400KW电机转子轴的堆焊修复[J]. 焊接技术.2001.2:10.
[8] 孙致祥.牵引电机转轴堆焊工艺[J].机车车辆工艺.1997.02.
[9] 王正坚.55KW电机轴的堆焊修复工艺.[J].机械.1993.04.
[10] 周国聘.ZQDR-410牵引电动机转轴堆焊.[J].机车电传动.1993.06.
[11] 徐滨士.装备再制造工程及失效分析.[J].理化检验(物理分册).2005.08:379~383.
[12] 华沂,吴益文,蒋海宁,等.多次再制造中加热对基体材料性能的影响.[J].理化检验(物理分册).2009.09:532~534.