摘要:钢锭模内表面浇注过程直接与钢水接触,表面的光洁度直接影响钢锭的表面质量、重复使用次数,由于钢锭模内表面曲线要求严格,一般不加工直接使用铸造表面,故对铸造表面质量要求很高,对各个影响因素须严格把控。
0. 前言
钢锭模的铸造方式全部采用砂型静态铸造方式,区别在于型砂材质的选择,外皮基本全部采用水玻璃砂铸造,芯核区别较大,目前常见选择型砂有三种,水玻璃砂铸造、树脂砂铸造、粘土砂铸造,其区别见表1
.png)
表1 钢锭模芯核造型用型砂区别
通过表1可以判断,如单纯考虑产品质量,首选树脂砂或者粘土砂造型,但目前铸造行业整体利润空间压缩,成本压力大,造成使用水玻璃砂生产的厂家逐步增多。
1. 钢锭模工艺流程
混砂→造型→刷涂→烘干→合箱→浇注→拆箱→精整→热处理,在制作流程中,从混砂到浇注环节对钢锭模内表面质量都有一定的影响,尤其是水玻璃砂造型生产中,有一点把握不好,极易造成钢锭模内壁重皮或者其他缺陷。
2. 主要工艺流程控制要点
2.1混砂
材料选择:石英砂粒度一定要适中,一般考虑选择30目—70目,各个目数区域百分比要均匀,严禁杜绝高目数或者低目数砂子集中;水玻璃模数要根据季节不同要有所区别,尤其是北方地区,冬季是水玻璃模数要适度提高。
混砂标准:在混砂过程中,根据砂子的目数适度调节水玻璃加入量,一般控制在8%—10%,根据砂子的粒度、形状等因素适度进行调节。
2.2造型
钢锭模铸造工艺设计中,排气方式是首要考虑的一个问题,主要是因为水玻璃砂浇注过程中发气量大,如工艺设计不合理,容易造成气孔等缺陷,由于钢锭模底眼直径较小,故采用下排气方式,同时芯核造型工艺由原三部分组成提高至四部分组成,由内到外依次为带骨架(采用带放气孔的焊管,依据芯核大小,直径随之变化)、其次焊管外裹草帘、草绳、报纸等易燃物、再次可移动松散物(碎砖、碎瓦等)、最终型砂(水玻璃砂),具体详见图1。
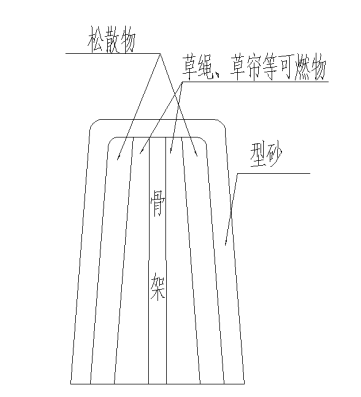
图1:芯核造型示意图
型砂造型完毕,起模后窑经过便携式硬度计检测,水玻璃砂一般要求达到85以上,否则容易产生粘砂现象,尤其是机械粘砂缺陷突出。机械粘砂系金属液渗入砂型或者砂芯粒间隙中,与砂烧结并粘附在铸件表面【1】。
2.3刷涂
芯核涂料以石墨涂料使用最为广泛,涂料由3部分组成:粉状石墨(45%)、片状石墨(45%)、粘结剂(10%),根据实际情况适度调节,粉状石墨主要作用于与型砂附着力、片状石墨主要作用于耐火度和防止粘砂缺陷的控制、粘结剂作用于涂料与型砂附着强度。
涂料厚度控制在3mm-5mm,过薄极易造成粘砂缺陷,过后烘干时容易裂纹浇注时造成渗钢缺陷或者结疤缺陷。为提高工作效率涂料一般采用刷涂方式,浓度控制在80-90波美度;特殊尖角、拐角部位最好抹涂料膏,以提高涂料强度和厚度,杜绝在铁水流动时突然改变流向造成涂料冲刷。
2.4烘干
水玻璃砂造型,相对粘土砂造型,水含量少,同时考虑成本问题,一般采用余热烘烤,针对大吨位钢锭模才入窑烘烤,烘干曲线如图2所示。
.png)
图2:烘干曲线示意图
烘干曲线高温区域一定要控制在200℃以下,否则极易出现型砂裂纹,会增加后期修补工作量,而且容易在此位置形成结疤缺陷或出现结合纹路,造成钢锭脱模困难。
2.5合箱、浇注
钢锭模合箱过程无特殊要求,唯一注意的锁箱、压箱要重点检查,因为钢锭模外形属于规则几何体,可以选择合适的砂箱,容易造成浮力大于重力,故锁箱、压箱环节多加注意。
铸件浇注原则一般是低温快速浇注,但钢锭模内壁属于不加工的使用面,在保证不粘砂的情况下,考虑适度提高温度,以增加铁水流动性,提高内表面的光洁度。
2.6拆箱、精整
带温度拆箱时,最好不要打水,容易增加清砂工作量;精整时任何小缺陷都不要放过,否则在使用过程中缺陷放大。
2.7热处理
钢锭模热处理为消应力退火,消除铸造应力,减少使用过程中的出现的裂纹概率、延长钢锭模使用寿命。退火曲线见图3
.png)
图3:钢锭模热处理曲线
3.结论
钢锭模的生产工艺决定钢锭模质量,钢锭模质量决定钢锭的表面质量,钢锭模工作面不进行加工致使对钢锭模生产工艺、操作要求较高,必须严把细节关,才能最终生产出合格的产品。
参考文献:
1. 史鉴开,史小雨 《铸造设备研究》 2006年4月 第2页
作者简介:
李仕源(1981-),汉,本科,高级工程师,主要从事铸造工艺研究。