庄 森, 陈 聪,文立刚
(山东省潍坊生建机械有限责任公司,山东 潍坊 261011)
摘要:采用化学分析、金相检验、力学性能和解剖分析等方法,对压缩机六级气缸体裂纹进行了分析。结果表明,设计不当导致应力集中是六级气缸开裂失效的主要原因,并提出了相应的改进建议。
关键词:气缸体;裂纹;失效分析;应力集中
1引言
某公司一台6MD20型氮氢气压缩机在使用过程中,先后多次发生六级气缸体开裂问题,开裂现象均为冷却水串气和缸盖螺纹孔漏气,事故对使用方和生产方都造成了不必要的经济损失。该气缸体使用材料为35号钢,锻造毛坯,正火处理;主要受力为活塞的往复力。为了找出气缸体开裂的真正原因,解除事故隐患,笔者受委托对开裂的六级气缸体进行了材质理化检验,并作了缺陷部位的解剖分析。
2理化检验
2.1宏观观察
此六级气缸体缺陷部位的宏观表现为气缸冷却水漏气。经探伤后发现,其开裂部位紧靠进气阀一侧,裂纹沿冷却水孔呈纵向弧状贯串三水孔长达160mm,见图1。



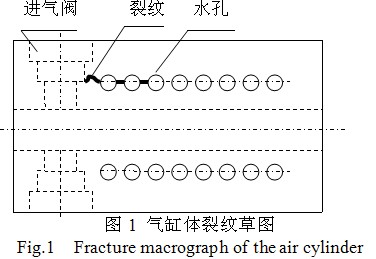



2. 2化学成分分析
在六级气缸体裂纹处取样进行化学成分检验,结果(质量分数)见表1。显然,其化学成分符合JB/T 6908—2006《容积式压缩机用钢锻件》标准中35号钢要求。故应排除由于材料成分不符合要求而造成开裂这一因素。
表1 六级气缸体化学成分(质量百分比,%)
Table 1 Chemical composition of the air cylinder sample(wt%)
元素
|
C
|
S
|
Si
|
Mn
|
P
|
测定值
|
0.36
|
0.018
|
0.35
|
0.62
|
0.012
|
标准值
|
0.32-0.39
|
≤0.035
|
0.17-0.37
|
0.50-0.80
|
≤0.035
|
2. 3金相分析
在气缸体裂纹处取金相试样,抛光后,在XJL-03型光学金相显微镜下观察,其组织结构为铁素体+珠光体,晶粒度为五级,非金属夹杂物为1级,无异常组织形式和晶粒粗大等现象。故亦应排除由于组织缺陷而造成开裂这一因素。
2.4力学性能
在气缸体靠近开裂处取试样,制成标准试棒后,在WE-300型液压式万能材料试验机上测试,其结果如表2所示,符合JB/T 6908—2006《容积式压缩机用钢锻件》标准要求的标准值。显然,其机械性能亦能满足要求。
表2 气缸体试棒力学性能测试结果
Table 2 Mechanical properties of the air cylinder sample
|
ReL/MPa
|
Rm/MPa
|
A(%)
|
Z(%)
|
实测值
|
345.5
|
620
|
23.4
|
47.5
|
标准值
|
≥225
|
450~590
|
≥16
|
≥32
|
3受力分析
六级气缸体工作原理:活塞的往复运行对来自五级气缸的氮氢气不断吸入、压缩、排出。由此可见,在工作中气缸所承受的内应力为变应力,而在变应力条件下,零件的损坏形式必是疲劳断裂[4]。疲劳断裂具有以下特征:疲劳断裂的最大应力远比静应力条件下材料的强度极限低,甚至比屈服极限低;疲劳断裂是损伤的积累,它的初期现象是零件表面形成微裂纹,这种微裂纹随着应力循环数的增加而逐渐扩展,直到余下的未断裂的截面积不足以承受载荷时,就突然断裂。影响零件疲劳强度的主要因素有:1)应力集中;2)绝对尺寸;3)表面质量。在表面质量经过检验没有问题的情况下,首先要考虑的是判断六级气缸体在工作中是否存在应力集中现象。
进气阀在缸径处的设计为圆孔,它在进气时受到由外到内的应力,它在压缩时由于进气阀已关闭,这时它受到的是由内向外的应力,这样就形成了方向相反的 “双周应力”,其分布都是沿圆孔圆周方向均匀分布,且都延伸集中到缸径的第一截面过渡处,这说明此处存在应力集中现象。
为了验证此分析,并找到真正的裂纹源和裂纹延伸的走向,在有关部门的配合下,笔者对气缸体进行了解剖。
4解剖分析
首先取下了进气阀门上部从阀盖到缸径的一部分,经着色检查,裂纹已沿缸径纵向扩展,横向已基本扩展到上端面(见图2),为了能找到真正的裂纹源,又将整个进气阀解剖下来,在对整个进气阀纵向断面解剖后,发现疲劳源位于阀腔距缸径的第一截面过渡处(见图3),裂纹沿90°尖角呈360°绕行一周,这和受力分析结果恰好吻合。从裂纹产生的过程来看,裂纹最初从尖角处扩展得很快,但当裂纹迅速地越出应力集中区后,其扩展速度反而降低;最后,由于疲劳裂纹的发展,使气缸体的有效截面显著减小,应力愈来愈大,裂纹扩展又再度加快,直至最后贯穿三水孔。从裂纹的延伸走向来看,其走向选择了沿强度较薄弱的方向,象缸径,冷却水孔道和缸盖的螺纹孔等,直到开裂,造成冷却水串气和螺纹孔漏气,最终造成产品失效。
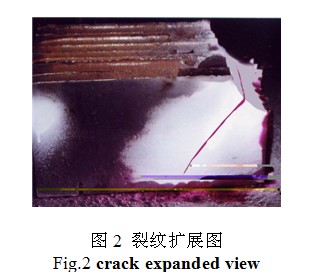
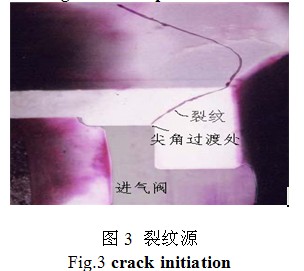
5结论
由金相组织、化学成分、力学性能检验可知,该气缸体本体夹杂物较少,组织合格,成分合格,力学性能合格,故排除因材料本身缺陷而造成开裂的可能。从解剖分析来看,裂纹是从进气阀距缸径的第一截面过渡处开始的(由图3可以清楚地看出),由此可以断定该事故为截面变化时尖角过渡在双周交变载荷的反复作用下,引起应力集中,从而产生的疲劳开裂。
6建议
(1)将阀腔距缸径的第一截面过渡处的过渡圆弧加大,并采用抛光工艺,以减小应力集中。
(2)将缸径上的圆孔改为腰形孔,以改变气缸在此处的周向均匀受力分布。
(3)设计部门重新验算复杂结构缸体的开裂薄弱部位(如缸径、冷却水孔道、缸盖螺纹孔等)的强度,确定最小安全尺寸。
7结果
科研部门采纳了上述建议,并对图纸进行了改进设计,现在为止新制作的缸体已运行超过20个月未再出现开裂现象。
参考文献:
[1]冯.弗里德里希.卡尔.瑙曼.机械器件和钢铁材料事故例集[M].北京:机械工业出版社,1987
[2]赵修领.圆钢纵裂分析[J].理化检验(物理分册).2004,8:424-426
[3]张勇.石油钻杆接头表面开裂原因分析[J].金属热处理.2004,29:76-78
[4]张德伟.KNT-30型齿轮泵转子国产化[J].流体机械.2004,8:34-36