赵仁顺,梁志农
(天津钢管集团股份有限公司,天津 300301)
摘 要:阐述了分层缺陷的检测原理,并根据分层缺陷产生的特点及在钢管中分布的位置,制作带有标准反射体的参考样管用于自动超声波探伤设备的动态校准。介绍了检测分层缺陷闸门的设置方法,通过对探头旋转速度、仪器脉冲重复频率、螺距等参数的设定,达到动态下稳定地检出参考样管上的标准反射体,实现对钢管管体分层缺陷的自动检测。通过现场实际检测验证了此检测方法的有效性。
关键词:自动超声波探伤;钢管管体;分层缺陷;标准反射体的制作;动态校准;闸门设置
API Spec 5L—2008管线管规范(第44版)要求对酸性和/或海洋服役环境的管线管管体要进行分层缺陷的检测,且规定了验收标准。国际上一些著名的大型石油公司如壳牌、美孚、沙特、道达尔、科威特等制定的管线管规范,甚至提出了比API Spec 5L更为严格的分层缺陷检验要求。为了保证分层缺陷的检测覆盖率并满足钢管生产企业的探伤节奏,应利用自动超声波探伤设备对钢管管体分层缺陷进行检测。
1 分层缺陷的定义
分层缺陷是一种通常与金属表面平行的、片状的内部金属分离。主要是由于钢坯中存在内裂纹、严重的疏松、残余缩孔、气泡及非金属夹杂物等造成的,会影响钢管的使用性能[1]。分层缺陷常出现在离钢管表面1/2~1/4壁厚处,在缺陷处剖分钢管,会发现横断面上有明显的层状分离,有些可分离成两层或多层,严重时会出现开裂,在裂缝处有肉眼可见的夹杂物,如图1所示。
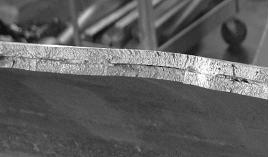
1—分层缺陷
图1 分层缺陷示意
2 分层缺陷的检测原理
分层缺陷应采用纵波直探头检测。A型脉冲反射式超声波探伤仪产生高频电脉冲,通过探头电缆线将脉冲电压加到探头晶片上,经过电/声转换,使晶片产生机械振动,通过耦合介质将此机械振动所产生的超声波传入钢管中,由于分层缺陷的存在,它与钢管的基体会形成声特征阻抗不同的异质界面,当直探头进行检测时,晶片发射的纵波到达声特征阻抗不同的界面,就会有一部分能量反射回探头晶片,将声能转化为电能,由仪器接收并进行信号处理,即会在超声波探伤仪示波屏上出现缺陷波和底波。水浸法(通常为自动探伤方式)的探伤图形如图2所示。
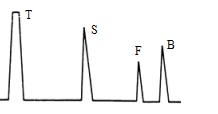
T—始脉冲(始波) S—界面波
F—分层缺陷回波 B—底波
图2 水浸法检测分层缺陷波形示意
3 标准人工分层缺陷的制作
结合分层检测方法标准ISO 10124—1994《压力用途的无缝钢管和焊接(埋弧焊除外)钢管 层状缺陷检测用超声检验》和管线管产品标准,决定按照API Spec 5L(第44版)标准中最严的酸性服役条件下的验收标准制作样管,标准反射体Φ6 mm平底孔,如图3所示。从钢管内表面刻制,深度为壁厚的1/4~1/2,最深不超过10 mm。设定扫描计划等相应的工艺参数,使用依据标准制作的带有人工缺陷的专用样管,进行试验后应用于实际检测中。
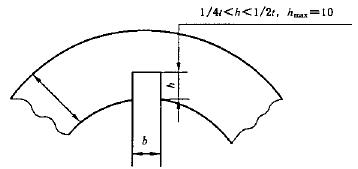
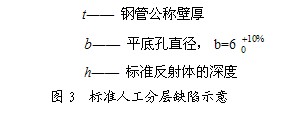
若标准反射体从钢管外表面刻制,假如深度为壁厚的1/4,则因为钢的纵波声速约为水的声速的4倍,所以,人工标准反射体的反射回波位置是分层缺陷实际位置的4倍左右。例如标准反射体深度是钢管公称壁厚的10%,则在示波器上的显示位置将在壁厚40%深度的范围,那么,实际检测分层缺陷的位置和样管上标准反射体的实际位置不一致。故分层缺陷的人工标准反射体只能从钢管内表面制作。
4 试验情况
4.1 试验条件
选用样管:Φ406.4 mm×10.5 mm 。
样管分层缺陷尺寸:从样管内表面加工一个深2.6 mm(壁厚的1/4),Φ6 mm平底孔。
试验使用德国GEIT ROTA 450S自动探伤系统,探头频率5 MHz,晶片尺寸32 mm×8 mm,单个探头有效声束宽度为10 mm,4个聚焦直探头,每个探头由4个并列的晶片组成,在旋转体上间隔90°均匀排布。水程距离大约为33 mm。
4.2 闸门设置
根据钢管壁厚和标准反射体的深度,分层闸门的设置(图4)分两种情况:
(1)闸门设置在一次界面波和一次底波之间,如图4(a)所示。
由于分层的深度只有壁厚的1/4,分层缺陷的一次回波L1与一次底波B1之间的距离很小,给闸门宽度设定带来很大困难,若闸门宽度设置较窄,很可能产生漏报;若闸门宽度设置较宽,一旦发生机械抖动,界面波S1或一次底波B1很可能窜入闸门而产生误报。
通过试验,如果分层深度大于1/4壁厚且深度大于2 mm时,底波的波动不易进入分层闸门。此时,将闸门设置在一次界面波S1和一次底波B1之间,分层缺陷的反射回波较高,信噪比较好,不易产生误报。
(2)闸门设置在一次底波B1和二次底波B2之间,如图4(b)所示。
当分层闸门设置在一次底波B1和二次底波B2之间时,通过现场实际调试,发现Φ6 mm平底孔的回波高度远远低于二次底波B2的回波高度(因为是二次缺陷回波)。为了防止分层缺陷的漏报,采用了DAC补偿的方法,只补偿分层闸门内的回波,避免了全壁厚补偿后造成信噪比达不到要求的弊端。同时,再次精确调整分层闸门的宽度,防止在机械波动较大时,二次底波B2跳入闸门产生误报。通过对检测速度、重复频率、扫描计划等相应参数的设定,可以满足现场实际检测的需要。
通过试验,若人工反射体刻制深度为钢管公称壁厚的1/2,通常可以把分层闸门设置在一次界面波S1和一次底波B1之间,标准反射体的回波较高,且能够避免因钢管抖动导致界面波或底波窜入闸门,保证分层缺陷的有效检出。
当然,在实际生产时,可以根据被检钢管的实际情况(主要是壁厚),设置分层闸门。分层闸门的设置不论采用以上哪种方式,根本的原则是不能产生漏、误报,确保分层缺陷的有效检出。
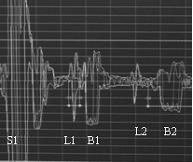
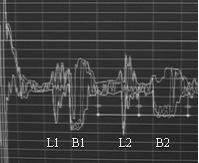
S1—一次界面波 B1—一次底波 B2—二次底波 L1—分层缺陷的一次回波 L2—分层缺陷的二次回波
(a) 设置在S1~B1 (b)设置在B1~B2
图4 分层闸门设置
4.3 技术参数的设定
4.3.1 确定最大旋转速度及脉冲重复频率(PRF)


式中 转数表示探头与钢管的相对转速;最大旋转速度为切向速度,即扫描螺旋线的线速度;有效脉冲间距为限定的目标有效脉冲间距;触发脉冲数为触发缺陷报警的脉冲数。
以上的2个算式可以保证圆周方向上的有效脉冲间距为1 mm,此有效脉冲间距的选择使钢管圆周上的扫查密度选取较为合理,从圆周方向上避免了缺陷的漏检。
4.3.2 根据螺距确定检测速度
检测速度的确定与螺距和转数有关,应按下式确定:
检测速度=螺距×转数 (3)
式中,检测速度—对于探头旋转,钢管直线前进的自动化探伤设备为辊道的速度;螺距即为探头旋转1周在钢管轴线上所走过的距离。
4.3.3 报警相关次数的设定
分层检测的难点就是对轴向和周向长度都较小的缺陷的准确检出,Φ6 mm平底孔的分层缺陷略小于晶片尺寸,这就意味着若检测速度、螺距等参数设定不匹配,就会产生漏检。如果钢管壁厚接近负偏差,一次底波B1的波动很容易就会跳入分层闸门,那么在正常生产时误报率会很大。通过现场反复试验,发现报警相关次数也是影响缺陷漏(误)报率的主要因素之一。设备可选择的报警相关次数范围为1~99,如果报警相关次数设定的很小,比如设定为1,即只要接收到一次报警信号就认为是缺陷,这样极易产生误报;如果报警相关次数设定的很大,比如设定为50,即一个缺陷要被探头捕捉到50次达报警门限才记为缺陷,这样就极易产生漏报。所以,应该设定合适的报警相关次数以避免漏(误)报。通过试验确认,当报警相关次数设定为5时,效果较好,漏(误)报率完全能满足标准要求。
检测分层缺陷常用参数见表1。
表1 检测分层缺陷常用参数
转数
/(r·min-1)
|
最大旋转速度(切向速度)
/(mm·s-1)
|
脉冲间距
/mm
|
外径
/mm
|
脉冲重复频率(PRF)①
/(次·s-1)
|
报警相关次数
|
500
|
5 733
|
1
|
219.10
|
5 733
|
5
|
500
|
7 146
|
1
|
273.10
|
7 146
|
5
|
500
|
8 475
|
1
|
323.90
|
8 475
|
5
|
500
|
10 626
|
1
|
406.40
|
10 626
|
5
|
500
|
11 963
|
1
|
457.20
|
11 963
|
5
|
注:①脉冲重复频率(PRF)数值为理论计算值,在表中其他参数确定以后,PRF不能超过表中所示数值。
在试验中,通过对试验结果的进一步分析,发现分层缺陷的深度越深越容易被检出,因此如果用户没有特殊要求,在满足标准及实际生产要求的同时,在制作样管时尽可能保证人工分层缺陷的深度。
5 实际检测
5.1 设备校准
按照ISO 10124标准,设备校准方式有2种:
(1)采用电子技术校准。将探头放置在标准样管上,在第一次底面回波满幅度下方10 dB处设定设备的报警电平。正常检验前,必须保证在设定的灵敏度下,能够检出图1所示的标准样管上的Φ6 mm平底孔。
(2)采用对比样管校准。在静态下,每个探头的中心依次对准对比样管上的平底孔,产生的信号满幅度作为设备的触发电平。正常检测时,选择适当的转速、钢管前进速度及设备脉冲重复频率,以检出标准允许的最小分层尺寸。
采用带有Φ6 mm平底孔模拟分层缺陷的对比样管调整设备各项参数,并按照正常探伤速度进行设备校验,对比样管连续3遍通过检测设备,样管上的人工分层缺陷均能很好的检出(图5)。
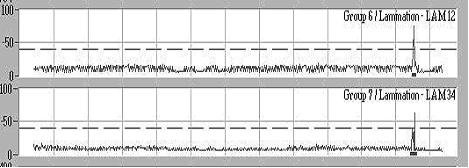
图5 对比样管校准带状波形
5.2 验收(缺陷处置方法)
如果缺陷的回波(荧光屏上显示的缺陷波高)大于或等于标准人工分层缺陷回波时,此支钢管应视为可疑品,采用手动超声波纵波方法确定分层缺陷的范围(即分层缺陷的面积),若小于标准相应级别允许的最小缺陷面积,则此分层缺陷是允许存在的,若超出则判废。
5.3 应用效果
经现场实际检测验证,此检测方法完全能够满足标准及用户的要求。目前,此方法已经成熟地应用于管体分层缺陷的超声波在线自动检测,完全满足生产线所要求的检测效率,同时保证了检测结果的可靠性。
6 结 论
(1)检测分层缺陷必须采用纵波垂直入射。设定好探伤系统主要参数,能够有效地检测出样管上的Φ6 mm平底孔(模拟分层的人工缺陷)和钢管中的实际分层缺陷,保证探伤结果的可靠性。
(2)检测分层缺陷的闸门可以根据钢管规格采用不同的设置方法。通常,将检测分层缺陷的闸门设置在一次界面波和一次底波之间。当人工反射体刻制深度较小时(一般小于2 mm),可以将检测分层缺陷的闸门设置在一次底波和二次底波之间。
(3)目前,此种检测方法能检测的钢管最小壁厚为5 mm,当壁厚小于5 mm时,检测效果不是很稳定。因此,在与用户签订生产技术合同时,对检测分层缺陷的钢管壁厚应双方协商。
7 参考文献
[1] API STD 5T1.Standard on Imperfection Terminology[S].1996.
赵仁顺(1969-),男,高级工程师,科长,主要从事钢管无损检测技术管理工作。